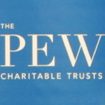
By Michael F. Carmichael
Nov. 8, 2012
On Dec. 16, 2012, the automotive industry will have its collective eyes focused on 2025 as a federal rule calling for that model year’s cars and light trucks to have a corporate average fuel economy (CAFE) of 54.5 miles per gallon takes effect. That translates to about 35-40 mpg in real-life driving - still a marked improvement over today’s results.
With gas costs fluctuating between $3 and $4 a gallon, and often spiking closer to $5, more and more new cars are getting close to the 2016 standard of 35.5 (again, in real-world terms, about 25 m.p.g.) today, so what’s the big deal?
It’s who is on board with that 20-mpg increase over nine years and why that matters.
![]()
|
A recent forum on fuel economy and innovation, sponsored by the Pew Environment Group’s Clean Energy Program, was held in the Automotive Hall of Fame in Dearborn, Mich. Led by Phyllis Cuttino, the program’s director, the forum featured representatives of an automotive think tank, an automotive supplier, a global engineering consultant and the United Auto Workers. That meant there were two PhDs, a Chartered Engineer (a UK designation) and a multi-degreed labor union executive. They were there to tell attendees how the industry is going to get to 54.5 by 2025.
Not at the conference were representatives of the automotive manufacturers. They are on record favoring them. The only industry group that’s unsure is the dealers.
Cuttino reminds the conference that the U.S. is exporting $1 billion a day to pay for our dependence on foreign oil. “That’s a risk to our economic security.” Additionally, the uncertainty of price volatility, taking oil “from as low as $35 a barrel to as high as $147, poses a significant risk to consumers at the pump.” It’s not just domestic consumers who have to deal with high fuel prices. As Corp! has noted earlier, the Department of Defense is actively engaged in a fuel economy program of its own. Beside the direct costs of fueling military vehicles, Cuttino raises another related aspect of importing oil: “The Rand Corporation estimates that we spend between $67 billion and $83 billion a year with the U.S. Navy to protect oil shipping routes. That is just another hidden cost to us at the pump.”
Cuttino further says that estimates show that the new CAFE standards will save the average motorist about $8,000 over the average life of a vehicle.
Turning to marketing, Cuttino pointed out that the global market for fuel-efficient vehicles is expanding at a rapid place and that the technology expertise gained in reducing the fuel requirements for American cars and trucks will be a plus in the marketplace in countries such as China and India. “We have got to invest in technology and innovation not only to keep up but to be able to export it,” she says.
What’s required in terms of technology and innovation to get to 54.5 by 2025 - and beyond? For that we turn to the panel members.
Brad Markell - International Representative, UAW
“While there are estimates that say the cost per vehicle will rise $1,500-$2,000, that’s more stuff,” Markell says. “That more stuff has to be engineered by somebody and produced by somebody. That equates to extra labor hours.” He explains as an example that for every 246 hybrid vehicles that are built to attain the standard another full-time equivalent job is created. Markell also points out that technology that has been developed here, but outsourced to foreign manufacturers, is being brought back to U.S. plants because it is considered ‘strategic’ sourcing. Ford, for one, has also discovered that doing so has saved it 20 percent.
There is strong and growing evidence about the link between innovation and manufacturing. “The old-school thinking was that innovation made the manufacturing base solid. Alan White of Princeton has written about this and says that if you lose manufacturing you lose innovation. As former Michigan Gov. Granholm said, ‘when factories leave engineers follow.'”
Jay Baron, PhD, president and CEO, Center for Automotive Research
“Light-weighting - aluminum, carbon fiber, specialty steel - is the technology that’s the common choice of all of the various pathways to get to 54.5,” Baron explains. “The main areas that are being explored as likely sources for light-weighting are the vehicle body, chassis, suspension and the powertrain - roughly 25 percent each of the mass of the vehicle.”
What’s a likely reduction in those areas? “Over the next ten to 15 years, 10 to 20 percent mass reduction is doable.” Part of that comes, according to Baron, “from high-strength, light-weight specialty steel in the safety cage, where we have a lot of safety requirements” to protect the occupants. “When you get away from the safety cage you can go to lighter weight components that are perhaps not as crash-worthy - but can still make the car safe.”
Another possible alternative for light-weighting future cars is a material that “every year you’re seeing more of - aluminum. You’re going to see aluminum doors in the next year or so,” Baron says. While stand-alone structures such as doors, hoods or deck lids are relatively easy to incorporate as lighter weight components, joining aluminum and non-aluminum parts creates corrosion issues.
That leads to another alternative, Baron explains. Composites (read: plastics). Perhaps Dustin Hoffman did get the right advice after all in “The Graduate.” There are big players in the chemical industry - Dow, BASF, DuPont, 3M, big multinationals - but “the auto industry is a little bit of an enigma to them. It’s a hard industry to get into. It’s mostly mechanical engineers you have to talk to. It’s stamping-intensive, it’s spot welding - this is a foreign language to the chemical guys.”
It’s a language that they may well be learning because they may bring some positive lightweight alternative solutions. “Urethanes, low-bond adhesives, a lot of unique chemical resins and things” that may well be adopted if both the auto folks and the chemical folks can learn each other’s languages.
To that end, says Baron, “We started a coalition at CAR called the Coalition for Automotive Lightweight Materials. Our mission is to promote a mixed-material car. The car manufacturers recognize that this is the ultimate solution to a lightweight vehicle.” One benefit coming out of the coalition, Baron thinks, is that the chemical companies may well serve as a catalyst (perhaps pun intended) in providing solutions to the aluminum-steel joining issue using a chemical adhesive. “The challenge here,” Baron explains, “is that the car companies have to be sure that the bond will hold up for the lifetime of the vehicle.”
Doug Baker, PhD, owner and CEO, TECAT Engineering Inc.
He’s a researcher in the area of engines. “That’s been my background. I think that the engine can contribute perhaps in the 20-30 percent range,” to attaining the 54.5 goal. Then he adds, “I wonder why the bar was set so low. But, that’s why I don’t set policy,” he laughs.
Baker is fond of diesel engines. He admits that years ago they were “smelly things that nobody would drive but many of you who’ve driven a diesel over in Europe will know that sometimes you don’t know what you’re driving.”
Whether diesel or more traditionally fueled engine, Baker says that he and his company are making great strides on a combination of engine design simulation and optimization. “We don’t get a lot of funding to build a bunch of prototypes,” he laughs, “so we have to do a lot of simulation. Much of my work is building an engine on a computer and then visualizing what that engine will do. We can optimize a hundred different engine sceneria in a matter of days or weeks through simulation. The question is: how good is the simulation? If everything makes sense you can really start to do some great optimization and move down the path to significant fuel efficiency pretty quickly.”
One of the “stealth” technologies that Baker is working with is the ability to perform real-time analysis of the amount of energy in fuel to make the vehicle go - the amount of work the fuel is doing. Currently, he explains, “it’s only about 30 percent. We want to put that kind of research into a controller that will optimize the vehicle while it’s going down the road.”
Andrew Smart, chartered engineer, director of the Automotive Headquarters, Society of Automotive Engineers International
Smart reminds attendees that fuel economy is not exclusively the domain of the automotive industry. “In the aerospace industry, fuel is one of the largest costs. Delta bought a refinery in Pennsylvania because they wanted to reduce the overall fluctuation in fuel prices. So, fuel economy affects all of us.
He prefers to fine-tune the idea of optimization by explaining that you can’t optimize a single element in a vehicle. “It’s really the optimizing of compromises that gets us to the final result.”
Smart, too, thinks that 2025 is “tomorrow. 2050 is the real goal. It takes about 20 years to replace the entire vehicle fleet, which is something that we need to do by 2050.” He says that there are too few “replacement cycles” between the 2014 model year and 2025 for that to be a realistic target date.
“We need to be increasing fuel economy by 1.5 to 2 percent every year,” he says.
Smart also underscores the value of a potentially diesel-powered passenger fleet. “There is more energy in a gallon of diesel fuel than there is in a gallon of gasoline, or a gallon of potential CNG [compressed natural gas] or LPG [liquefied petroleum gas].” He explains “only 20 percent of the energy of the fuel goes into driving the engine. That’s enough to focus the mind.”
Engine downsizing, from V-8s to 6 cylinders to often-turbocharged 4s, is yet another way to get to 54.5 Smart says. “But it’s only the first wave. We’ll be looking at some sort of electronic supercharging because the customer will accept no compromise when it comes to drivability.”
Today’s engineers are working hard at replacing mechanical connections with electronic ones because, Smart explains, “when you take a load off the engine you can reduce the size of the engine. When you reduce the size you reduce the mass.”
Turning to the transmission, Smart notes that the number of gears available has gone from “three speeds on the steering column to four, six and currently nine gears. What can you do with nine gears? A lot. What you’re doing is keeping the engine at a more efficient point for longer.” But, he cautions, adding gears shouldn’t be noticeable to the driver or “the J.D. Power ratings are affected.”
There are a lot of smaller incremental changes in a variety of systems that can increase fuel economy by 1 to 2 percent. One is by reducing engine idle time by stopping and restarting the engine when it’s idle for more than a set period of time. The only problem there is “the conventional engine is used to being started 40,000 to 50,000 times during its lifetime. If I put start-stop in there it could be started half a million times, and with hybrids it could be a million times. So, it’s not as simple as it sounds.”
Citing another example, Smart notes that by using a global vehicle platform manufacturers are able to save money. But, by using different propulsion systems in that platform there have to be changes made to the “crash signature” - you can’t just drop an electric engine in place of a conventional one without changing that signature and reconfiguring the way the engine, and the occupants, react in a crash. That’s a factor that needs to be added to the cost-saving calculation.
Despite America’s newfound sources, there are still far more competitors for carbon-based fuels across the globe - particularly in the so-called developing nations. Fossil fuel is a finite resource.
54.5 mpg by 2025 is attainable, experts say, and, should the incremental technological innovations discussed by the Pew panel be implemented - as the major automotive manufacturers say they will do - it may will be an affordable and positive step toward a future less dependent on that finite resource.