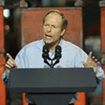
By Michael F. Carmichael
Feb. 23, 2012
The final quarter of 2011 saw the U.S. manufacturing sector experience modest, yet still unexpectedly strong growth. Many economists predict that will continue this year. Factory workers put in more than 40 hours a week on average, the first time that’s happened since the late ’90s - leading to an expectation that new manufacturing hires will continue. The jobless rate continues to decline amid other positive signs that seem to indicate an improving economy.
In Europe, of course, that’s not the case. And, in Asia, an expanding economy is leading to higher labor and logistical costs - both of which are causing some American manufacturers to revisit earlier decisions to outsource manufacturing to the area.
And, it’s reinforcing decisions made by others to keep their manufacturing here in the first place.
![]()
|
Insourcing
Master Lock CEO John Heppner was one of those singled out at President Barack Obama’s State of the Union address. He and the company he heads were at the joint session of Congress representing a trend the president hopes will grow over the next few years. To emphasize the importance of what he calls “insourcing” - jobs that were previously outsourced to other countries - the president visited a Master Lock factory in Milwaukee on the day after Valentine’s. As the president was taking a tour of the production area, Heppner was warming up the crowd.
Commenting that he was nervous about what the employee taking the president on the tour might say, Heppner exclaimed, “God knows, the president could come back a Republican.” As the workers broke into raucous laughter, Hepner continued, laughing, “Did I really say that?”
The 500 employees and visitors gathered in front of a temporary podium were excited that the president was “in the house,” to use one of his expressions. Heppner was definitely into the spirit of the occasion and sincerely proud of his employees.
“We went through hell together, did we not - and back!” Heppner exclaimed, talking about the rocky previous years, and pausing as he addressed his audience. “I just thought of all the lost production over the last few days.” He paused again. “I can always bring in a few locks from China to make up the difference,” he said as the crowd booed heartily. “Okay, I’ll take it back.”
Turning serious, Heppner continued with obvious emotion, “We figured out how to make this facility productive. You guys helped us. We worked together. Today, it’s about trust. We care more about our mutual success than our own. Because we did it, we have the president of the United States, Barak Obama, here to recognize what we’ve done. I love you all!”
![]()
|
After the usual thank-you’s and topical humor - including remembering how he was constantly forgetting the combination to the Master Lock on his gym locker in school, - the president got into his remarks, “I’m here today because this company has been making the most of a huge opportunity that exists right now to bring jobs and manufacturing back to the United States,” Obama declared. “Over the past few decades, revolutions in technology have made a lot of businesses more efficient and more productive. And that’s a great thing. But, as some of you know, technology has made a lot of jobs obsolete. And, it’s allowed companies to set up shop and hire workers almost anywhere in the world. Too many jobs that provided a decent living got shipped overseas.”
“Over the past few years it’s become more expensive to do business in countries like China. Meanwhile, American workers have become more productive. So when John Heppner was at the White House in January, he told me how it makes more business sense for Master Lock to bring jobs back home here to Milwaukee. And today, for the first time in 15 years, this plant is running at full capacity. Today, you’re selling products directly to customers in China stamped with those words: Made In America.”
Heppner had said in January that a number of factors entered into his decision-making process to return work to Milwaukee. An improved labor cost structure was one of them, as was a desire to be able to respond quickly to customer demands - such as being able to deliver custom products quickly without having to wait for container ships to arrive from China.
Retaining
Across Lake Michigan, another global player in the manufacturing sector is Grand Rapids-based American Seating.
|
While the President went to Milwaukee and Master Lock to talk about bringing jobs back, in January Vice President Joe Biden visited Grand Rapids to underscore the importance of keeping American manufacturing jobs in the country. Why American Seating?
The chances are much better than even that you have sat in a variety of American Seating products, probably from the time you were in grade school. For more than 125 years the company has produced school desks, portable seating that changed gym floors into auditoriums, seats for buses and trains and sports stadia such as the friendly confines of Wrigley Field - almost anywhere Americans sit.
And, it’s been Americans making those seats.
Deb McDermott is vice president of marketing at American Seating. “When the vice president’s advance team visited they were initially focused on our transportation seating but they were amazed at the breadth of what we do,” she says. “When I told them that we had done the seating at the Washington Nationals stadium, as well as the Eisenhower Theatre in the Kennedy Center, they were surprised.”
![]()
|
McDermott says keeping jobs in Grand Rapids has been a challenge. “We’ve had to take a hard look at it, but we’ve always made the commitment to stay local and stay with the community.”
Commitment is one thing and dealing with economic reality is another. How does American Seating do both? “We try to keep our costs in line. We try to do strategic sourcing and make sure that we’re making the best sourcing decisions. Just trying to make sure we’re delivering the best value to our customers.”
Citing her company’s brand promise, McDermott says they make “a quality, durable product. We’ve been in business 125 years because we make products that last.” Some of those Wrigley Field seats seem as though they’ve been there from when the ivy covering the outfield walls was just sprouting.
When McDermott spoke about strategic sourcing she meant not just strategic, but local. “Our materials spend is about 75 percent from Michigan, Ohio and Indiana. Ninety-five percent of our total materials spend is domestic.” The local sourcing, then, ties back to keeping costs in line. “It reduces our shipping costs.” There’s another consideration as well, she says. “From an environmental standpoint it’s good.”
The company plans to stick to its core markets as it grows, McDermott says. “We’re making a significant investment in growing our business through product development - but I can’t talk to you about it yet.” She can, however, talk about one of them - higher education - particularly community colleges. “The learning has shifted a bit and we have adults going back to school to get a second degree or new training or even an associate’s degree. With the economy the past few years the community colleges have seen quite a bit of growth.” Some of the demand for new seating results from the fact that older students returning to the classroom are, well, larger than their younger counterparts. “Yes,” McDermott agrees with a laugh, “there’s that growth as well.”
While other folks have been turning to community colleges to learn new skills, McDermott says that “since about 2006 the manufacturing core workforce has been pretty steady.”
![]()
|
American Seating’s head of human resources Paul Dieterle confirms that. While the company is constantly improving the way it builds products, it relies primarily on providing in-house training. “Most of that is in the context of using trained, experienced operators and have them bring along someone who’s new to the area on the tasks and requirements for the area.”
Dieterle further explains, “We have a registered apprenticeship program with the Department of Labor and that is our preferred way to fill skilled trades jobs as they open up. We also send employees to specialized training as required.”
Master Lock, too, concentrates on having a well-trained workforce. That can be a challenge, says CEO Heppner, who takes a larger view of future manufacturing needs. “The number of young people exposed to skilled labor trades through education or family and friends is declining while our current skilled labor workforce is aging. At Master Lock, we partner with trade schools and other educational institutions to help inspire young workers to choose careers in skilled labor. We encourage our government and other businesses to engage with these organizations and invest in training future generations in skilled labor careers.”
Toward that end, Heppner continues, “Master Lock has established partnerships with local technical colleges and universities to help them improve their recruiting and curriculum development to encourage students to train for skilled labor jobs.”
The bottom line is dependent on providing a strong educational foundation for the American manufacturing workforce, experts say. Whether it’s an entry-level job or retraining for a different - more technologically demanding - environment, the challenges of the average worker have changed considerably over the past generation. The ability of that workforce to adapt and grow in a rapidly evolving and highly competitive global marketplace will play a significant role in the country’s future success.