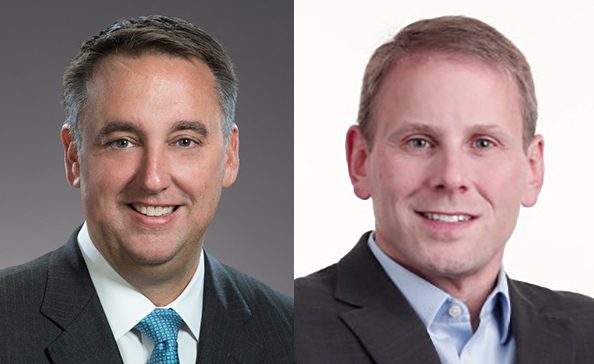
Steve Wybo figured the United Auto Workers strike – now more than 40 days old – would likely last through Thanksgiving, but that the projection could change if the UAW began targeting the more profitable plants that produce the Big Three’s most popular vehicles.
On Oct. 11, the UAW struck Ford’s Kentucky Truck Plant, which builds F-Series Super Duty trucks and a pair of SUVs: the Ford Expedition and Lincoln Navigator, which generate about $25 billion in revenue each year.
On Monday, the UAW sent 6,800 members to the picket line at Stellantis’ Sterling Heights (Mich.) Assembly Plant, where Stellantis’ best-selling vehicle, the RAM 1500 truck. Then, on Tuesday, the UAW hit one of General Motors’ most profitable plants, the Arlington (Texas) Assembly Plant, where GM builds the Chevrolet Tahoe and Suburban, Cadillac Escalade and GMC Yukon big SUVs.
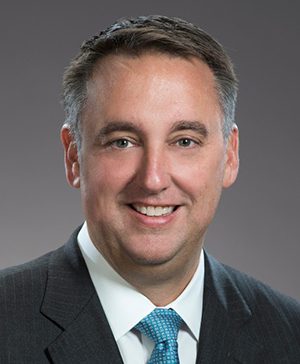
“I think it goes until at least one, if not all, of the big trucks go down,” Wybo, a senior director at Riveron who deals with automotive strategy and automotive turnaround, told Corp! Magazine last week. “Then it probably settles pretty quickly after that.”
On Wednesday, Wybo was proven at least partially correct when Ford and UAW announced they’re reached a tentative agreement.
But there’s been no word on potential settlements with either GM or Stellantis, although information trickles out on potential offers being made by the automakers. Which means the strike continues on for them.
But Wybo and other experts aren’t really worried as much about the automakers as they are for the lesser-known victims of the strike. While the Big Three and, to a lesser extent, the larger Tier 1 suppliers impacted by the strike should come out of it OK, the smaller suppliers – Tier 2 and Tier 3 companies – are likely to have a harder time, especially if the strike is an extended one.
“Four weeks, not a big deal … eight weeks? A lot of folks live paycheck-to-paycheck, and I would say a lot of them don’t have two months of dry powder sitting around their bank accounts,” said Wybo, who specializes in, among other things, insolvency/bankruptcy matters, turnaround and crisis management, profit enhancement, mergers and acquisitions and business valuation. “Once their lifestyle has to be adjusted, once it gets cold – striking in snow and sleet and rain is not fun – those all factor into the decision making.”
Wybo, who took part in a panel discussion at a recent Association for Corporate Growth event dedicated to the auto industry, said most of the discussion leading up to the strike was about how it would impact the automakers and how it could cost them billions of dollars.
It’s the effect the strike will have on the supply base that doesn’t get talked about as much.
“What we haven’t heard a lot about is the trickle-down impact it’s having on the supply base,” Wybo said. “The supply base came into the strike very challenged from a financial standpoint. If you think about the last 3-4 years during Covid, the OEMs produced very good profits on low volumes because the average selling price of a vehicle has gone up about about $7,000 since Covid hit. They’ve been able to sell these very expensive units to … the consumer.
“The supply base doesn’t have that luxury,” he added. “They sell to GM and Stellantis and Ford and everyone else at a fixed price. All of their costs have gone up – raw materials, labor, insurance, utilities, you name it – inflation has hit these suppliers hard. (But) it’s a B-2-B business, so suppliers don’t have the ability to go to (the consumers).”
Mike Wall wholeheartedly agrees. Wall, the executive director of Automotive Analysis for S&P Global who has done financial analysis of the auto industry for more than 20 years, said the auto industry is going through a “radical transformation,” when so much focus is directed at the electric vehicle market, and at a time when suppliers are “extremely challenged.”
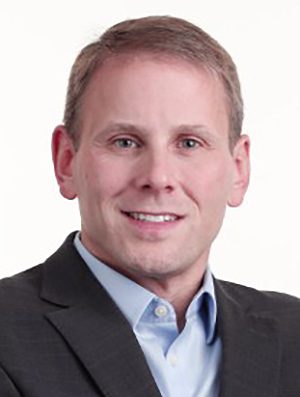
“We went through one year of Covid in 2020, then we saw supply chain challenges, we saw a rampant runup in commodity costs, shipping and logistics costs. We saw interest rate hikes and we saw inflation,” said Wall, who sat on the ACG panel with Wybo. “All of this has battered suppliers over the last three years. Production in the region in 2020 and 2021 were at recessionary levels. They weren’t all that much better in 2022; they were improved but still weak. And then you come to this year. We’re finally getting our legs under us from a production standpoint and the strike happens.
“When we talk about the state of the supply chain, it’s stressed, it’s challenged already,” Wall added. “Couple that with the fact we have all of these EVs coming down the pike … Suppliers have to plan for them, have to build tooling, prepare their production lines … and yet EVs are still a nascent technology, a nascent segment where the volumes … are going to be more volatile, or at least may not all hit. All of this is taking up the attention of the supply chain, and then you have the strike. That just adds a whole new wrinkle to the conversation.”
“If this strike drags on, and more importantly if it starts impacting high-profile plants, it’s going to introduce a new level of stress to the supply chain that we haven’t seen … since the Great Recession.”
Statistics appear to be bearing that out. The most recent survey from MEMA (Motor & Equipment Manufacturers Association) Original Equipment Suppliers shows the vehicle supply base “continues to feel impacts” from the ongoing strike.
The survey, conducted Oct. 16-18 and reported on aftermarketnews.com, showed :
- Concerns over sub-tier financial viability remain heightened, with 79% of all suppliers surveyed indicating they are concerned.
- The percentage of smaller suppliers that areconcerned with their internal financial viability increased dramatically to 42%.
- Supplier estimates of the ramp-up time to get facilities back to pre-strike levels has increased to 1.5 weeks; the greatest challenges to restarting operations remain retaining labor and material availability.
- Of the 84% of suppliers that have received cancelled ordersfrom their customers, 95% indicate they have received short to essentially no notice.
- The percentage of suppliers that have laid off their direct and indirect labor employees remains essentially unchanged maweek over week, with 80% of suppliers who have yet to begin layoffs indicated they will begin in early November if the strike is not resolved.
According to MEMA, vehicle suppliers employ more than 900,000 workers, over six times more than the 146,000 UAW Detroit Three automakers. Suppliers also contribute 2.5% of the U.S. Gross Domestic Product (GDP) and operate in all 50 states.
So it was already hard for the Tier 2 and Tier 3 suppliers. Now that the UAW has started hitting plants where the profitable, more-popular vehicles are being produced, Wybo figures things could go downhill from here.
“It’s getting worse by the day, and you’re reading every other day there’s a new supplier who had to furlough people … laying people off,” he said. “The longer this goes the more that’s going to happen. They’re trying to work with the supply base but overall it’s getting worse and worse and worse.”
Wall calls the Tier 2 and Tier 3 suppliers the “lifeblood” of the auto industry. Hurting them is likely to do significant damage to the industry writ large.
“Obviously the automakers get the accolades … but the rubber hits the road with the Tier 2 and Tier 3 (suppliers),” Wall said. “They’re building the sub-compondnts, the pieces and parts that go into these vehicles. If those suppliers go down, it wreaks havoc in the supply chain.
Both experts think the suppliers should have, and did to a certain extent, built strike plans, particularly as the rhetoric surrounding a potential strike heighted earlier this year. But, as Wall said, leaders can’t prepare for every eventuality,
“I’m polyanna about this … every four years we go through this kabuki dance, but this rhetoric took on a whole different tone and tenor,” he said. “I think it’s fair to say suppliers leading up to the deadline were crafting strike plans (but) there’s only so much you can do … there are some limitations to what you can do to isolate the impact. Suppliers were going in with pretty open eyes.”
Wybo agrees businesses did what they could to prepare to the extent they were able. Still, plans can take a business only so far.
“Everyone knew this was coming … When the rubber hits the road and you have to send people home and you look in your bank account and see you have three weeks of payroll to cover. Then in Week 4 you have to tell (workers), ‘Hey, I can’t pay you your paycheck any more,’ then it becomes real.”
That situation can get laid-off or striking workers wondering if they should, instead, ‘go work at Amazon warehouse and make maybe a little more than I was making with you?’ Wybo draws the comparison to the early days of Covid, when people were home collecting unemployment or other government assistance.
“A lot of workers were comfortable sitting on the couch and collecting unemployment and government assistance,” he said. “We had the ‘Great Resignation,’ and it took awhile to get people back to work. That money ran out and people said ‘I gotta go back to work.’
“We were just getting into a good cadence, absenteeism was starting to come down, labor was getting better than it was a year ago, and now we’re sending people home again,” he added. “They’re going to remember that couch was comfortable. It could take awhile to get ramped back up again.”
This all comes at a time when the industry is running on thinner margins to begin with, particularly among the suppliers. The industry was back to a semblance of normal, with no rampant inflation, not semi-conductor issues, and the carmakers were averaging about 16.5 million units sold a year. Then, in March 2020, Covid shut the world down.
Now margins are a lot smaller, according to Wybo.
“The world changed in 2020 and we haven’t made any money since,” he said “Margins are down at least 20% on a composite average for the entire supply base since 2019. That just makes sense, you don’t have to be a financial wizard to think volumes are down 3-4 million units a year for four years in a row, the price of everything has gone up, so you have less contribution margin coming from less parts, so you must have less profits.
“The vast majority of suppliers are about 20% or worse less profitable than they were in the last clean year we had in 2019,” he added. “The OEMs are more profitable.”
The problem for suppliers is they don’t have the ability to make up for lost profit margins by going to the consumer, the way the automakers did. They have contracts that provide for a fixed price for the goods they sell to the car companies ane the large suppliers.
“Suppliers don’t have that kind of pricing power,” Wall said. “If their costs go up, they can approach the automaker or their Tier 1 supplier and say, ‘My price has gone up, I need your price to go up.’ In many cases that automaker … is going to say, ‘good luck with that.’ It’s part of the conversation. The time for those conversations was probably a year or two ago, but those margins have been crushed so much that those conversations are still going on.”
Lurking on the fringe of the entire discussion is the EV industry, which appears to be hitting some bumps in the U.S., despite a huge push from the car companies and the Biden Administration to move toward that technology. Suppliers have felt the pressure, according to Wybo, with the car companies telling them they’re going to launch a record number of units over the next four years.
That forces the suppliers to invest capital in facilities and equipment, because they want to be in on supplying for the popular EVs, like the Silverado or the F-150 Lightning.
But now, the carmakers are saying “hold off,” he said. For instance, GM recently announced they’re delaying production at their Orion facility by a year.
“If you’re a supplier that tooled up for that because you thought you were going to launch next year – you start to train people, you put capital on the floor, you’ve got a nice new facility – and GM says, ‘Sorry guys, we’re going to kick that a year out.’ That’s a huge problem. Now you have all this capital tied up in machinery and equipment doing nothing. It’s producing no value.”
Wall looks at EV sales, which he said are “up this year versus last year.” EVs are still growing, he said, but the problem is there may be too much product.
“It’s almost like the activity and the deployment overwhelming consumer demand,” he said. “That’s kind of masking some of the impact. The reality is we have a lot of product coming down the pike. It’s a blessing and a curse. The blessing side is we have a lot of consumers who are going to have a bevy of offerings to choose from. The challenge is there may not be as many consumers; we may be chasing consumers with products for awhile.”
EV battery and vehicle platform specialist Proterra became the latest company to have filed for Chapter 11 bankruptcy. That forced Sweden-based Volta, which got its batteries from Proterra, to release a statement saying Proterra’s decision “had a significant impact on our manufacturing plans, reducing the volume of vehicles that we had forecast to produce.”
“The uncertainty with our battery supplier also negatively affected our ability to raise sufficient capital in an already challenging capital-raising environment for electric vehicle players,” the statement read.
That kind of uncertainty is likely to hinder the Biden Administration’s stated goal of 100% EVs by 2035, a goal Wall called a “tall order.”
“That’s … not in our forecast,” Wall said. “100% would be a tough one. Our estimation right now, which is pretty robust, is that by 2035 we’re closer to 79%, which is a pretty strong number in its own right. There’s a lot of puzzle pieces that have to fall into the right place, not the least of which is charging infrastructure. It’s a tall order.”