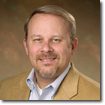
By William Doyle
April 8, 2010
More than 40,000 types of commercial products are made from natural rubber latex (NRL)-from gloves and condoms to balloons, mattresses and pillows. It’s been estimated that 3 percent of the general population suffers from some form of latex allergy, thus hindering their ability to use these and other products. Yet a remarkable new technology is not only capable of removing virtually all of the proteins in latex that cause allergy symptoms, but also saving precious water and energy in the process.
What keeps this new form of modified latex a green material? The answer lies in how it is made. A key step involves the addition of aluminum hydroxide, a well-known protein binding chemical, to the latex while it is still in liquid form. The aluminum hydroxide attracts and binds proteins to it, and the resulting protein complexes are later flushed out of the latex. Traditional production of manufactured products involves the reduction of proteins from latex through cycles of washing and/or leaching. With the use of the modified natural rubber latex, with its starting ultra low protein levels, the reduction or elimination of these secondary processing steps can be accomplished, saving significant water and energy resources and reducing costs.
In addition to the above, the new form of modified NRL is derived from the rubber tree Hevea brasiliensis and is 100 percent biodegradable. In contrast, many synthetic alternatives, such as PVC vinyl, styrene, nitrile, choloroprene and polyurethane-made from petrochemical derivatives-are neither biodegradable nor compostable. Unlike these synthetic alternatives, the modified NRL has minimal impact on the environment, much as an oak leaf.
One study conducted at a latex surgical glove manufacturing plant in India brings these facts to life in a vivid way. During a period when the plant was producing 110,000 pairs of latex gloves per day, it was found that the amount of water consumed during the traditional rinsing and leaching procedure associated with standard NRL was 36 kiloliters per day. In comparison, the use of modified NRL required only 14.4 kiloliters per day. The difference amounted to a cost savings of $108,000 annually. At the same plant, the daily energy consumption associated with the use of standard NRL amounted to 684,000 kilocalories per kilowatt-hour; the corresponding figure for modified NRL was 288,000 Kcal/Kwh. Here the annual savings came to $364,500. Summing these figures shows that the plant could save itself a total of $472,500 with the use of modified NRL while being greener as well.
Water is not only important to human survival, but to many sectors of the economy. The future of any society and business depends on the preservation of water resources as part of the sustainable development process. Companies need to think about how much water they are using and consuming. The true cost of manufacturing is measured as the sum of the total costs throughout the production cycle, and sometimes more can be less. Water and energy stress caused by the growing global population is expected to reach historic proportions, driving supply down and costs up, and directly affecting business operations according to a recent United Nations report.
As we’ve seen above, the new modified NRL offers a greener alternative to standard NRL-a definite plus in an environmentally conscious world in which businesses are increasingly seeking to conserve water and energy.
William Doyle is chairman, president and CEO of Vystar Corporation and has co-authored and presented numerous papers for Vystar globally.