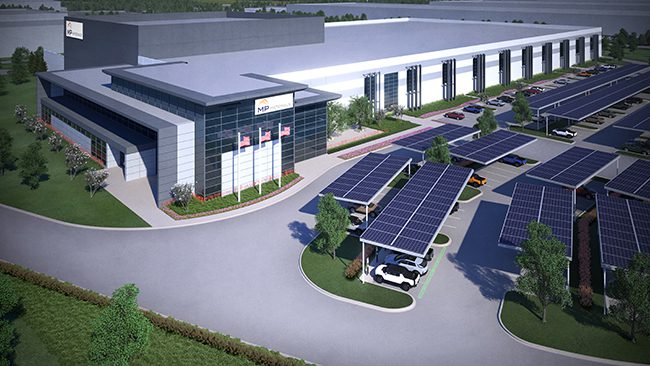
DETROIT AND LAS VEGAS – General Motors (NYSE: GM) and MP Materials (NYSE: MP) today announced the formation of a strategic collaboration to develop a fully integrated U.S. supply chain for rare earth magnets. Under the long-term agreement, MP Materials will supply U.S.-sourced and manufactured rare earth materials, alloy and finished magnets for the electric motors used in the GMC HUMMER EV, Cadillac LYRIQ, Chevrolet Silverado EV and more than a dozen models using GM’s Ultium Platform, with a gradual production ramp that begins in 2023.
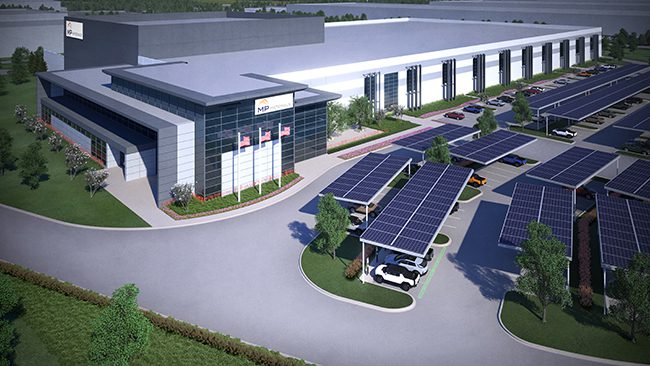
Neodymium-iron-boron (NdFeB) magnets are critical inputs that enable electric motors to transform electricity into motion. Although development of permanent magnets began in the U.S., there is virtually no domestic capacity to produce sintered NdFeB magnets today. This strategic collaboration seeks to accelerate the restoration of the U.S. rare earth supply chain at commercial scale with high resiliency and environmental sustainability.
MP Materials owns and operates the Mountain Pass rare earth mine and processing facility in California, the only active and scaled rare earth production site in America. Rare earth materials sourced from Mountain Pass will be transformed into metal, NdFeB alloy and magnets at a new production facility MP Materials today announced it will build in Fort Worth, Texas, delivering an end-to-end, U.S. supply chain.
“We are building a resilient and sustainable EV manufacturing value chain in North America, from raw materials to cell manufacturing to electric drive motors and beyond, further accelerating GM’s vision to support a mass market for EVs,” said Shilpan Amin, GM vice president, Global Purchasing and Supply Chain. “Our work with MP Materials is another bold step forward that will help ensure that we meet our goal to lead the EV industry in North America in more than just sales.”
“Restoring the full rare earth supply chain to the United States at scale would not be possible without U.S. manufacturers like GM recognizing the strategic consequence and acting with conviction,” said MP Materials Chairman and CEO James Litinsky. “We are proud to welcome GM as the foundational automotive customer for our new magnetics facility and join forces with a company fully aligned with our vision to reinvigorate the American manufacturing spirit.”
GM and MP Materials have signed a binding agreement on terms and expect to enter into a definitive supply agreement shortly. In addition, the two companies will look to collaboratively engage from a public policy perspective to seek policies that are supportive of the establishment of a secure, U.S. rare earth supply chain.
Integrated recycling and environmental sustainability
MP’s domestic supply chain spanning California and Texas will provide certainty of provenance, supply and sustainability. Mountain Pass is a closed-loop, zero-discharge rare earth production facility with a dry tailings process that recycles more than 1 billion liters of water per year.
To optimize for efficiency and sustainability, waste generated during MP’s rare earth alloy and magnet manufacturing will be recycled back into the process. GM and MP Materials will also explore the potential to further optimize production efficiency and conserve natural resources through novel recycling approaches based on end-of-life, closed-loop principles.
GM EV Milestones
- Invest $35 billion in EV and AV product development by 2025
- Launch more than 30 EVs globally through 2025
- Sell more than 1 million EVs globally by 2025, earning EV market leadership in North America
- Drive first-generation Ultium cell costs 40 percent lower than those used in the Chevrolet Bolt EV; achieve twice the energy density at 60 percent lower cost in the second generation
- Rapidly scale EV manufacturing, with more than 50 percent of North America and China plants capable of EV production by 2030
- Double annual revenues from a five-year average of about $140 billion by the end of the decade, expand margins, and grow EV revenue from about $10 billion in 2023 to approximately $90 billion annually by 2030