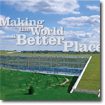
By Joseph P. Cadabas
Jan. 28, 2010
This year’s Corp! Going Green Award winners range from automotive suppliers to alternative energy companies, a hotel, a laundromat, dentist’s office, architects, IT firms and a farm. All are worthy of recognition as Michigan’s environmentally conscious leaders for their sustainable business practices, education programs, and daring in a number of green initiatives.
The program includes three categories: Green Initiative Champions, Green Industry Innovators,and Green Organizations.
Green Initiative Champions- including a law firm, a recycling company, and a mortgage title agency - implemented green and sustainable business practices, technologies and methodologies. Many of the Champions have used green construction and building renovation practices to meet the requirements of the U.S. Green Building Council’s Leadership in Energy and Environmental Design (LEED) designation.
Green Industry Innovators included a bus tour company, chemical suppliers, and retail and gift card firms. They offered green services and/or products. The Green Organizations include universities, community organizations and nonprofits who are either promoting or advocating for environmental sustainability or have engaged in green initiatives themselves.
Some of the nominees have received previous awards or federal government recognition, including from the U.S. Environmental Protection Agency (EPA). We hope you’ll glean some green ideas of your own from our winners.
Green Initiative Champions
American Seating
www.americanseating.com
A year ago, American Seating began using a new and more environmentally-friendly metal pre-treatment process that reduced water usage and cut the release of phosphate chemicals, a potentially harmful nutrient that ultimately ends up in waterways. “At American Seating, one of our guiding company principles is: ‘To be responsible stewards of the environment by utilizing materials and manufacturing processes that are sustainable and lessen our impact on the planet,'” notes Ed Clark, company chairman and CEO. The new pre-treatment process for metal components replaces iron phosphate with a zirconium conversion coating technology before the application of the final powder-coat paint. The City of Grand Rapids Wastewater Treatment Department was highly supportive of the company’s change-over. American Seating no longer discharges phosphates into the sewer system. Additionally, the new pre-treatment reused most of its existing equipment with only a few modifications, preventing scrappage. American Seating reduced its energy consumption because the new treatment chemicals and rinses do not need to be heated above ambient temperatures. “Some define going green as using as much post consumer or post industrial content in products as possible,” Clark says. “Others define it as developing products with components that are recyclable. Still others define green by the manufacturing processes used to create products. We are striving to better understand the opportunities to evaluate sustainability on a corporate level, and we are committed to continuous learning.” American Seating was the second business in Grand Rapids and among the first in Michigan’s contract furniture industry to switch to the zirconium pre-treatment process.
Bodman LLP
www.bodmanllp.com
![]()
|
One of Detroit’s long and storied law firms, Bodman LLP, implemented a series of best practices for office paper management and other energy-saving initiatives that impacted many aspects of its operations during the past year. In recognition of its sustainability actions, in August 2009 the American Bar Association awarded Bodman the coveted “Law Office Climate Challenge Partner” certificate. “Our greatest challenge when making business decisions is giving environmental factors as much priority as pure economic ones,” said Ralph E. McDowell, the law firm’s chairman. “Sustainability requires that social and environmental factors be part of the decision making process, and this can have both economic and environmental benefits.” Bodman’s sustainability initiatives include: installing water filtration devices for normal tap water and discontinuing the use of bottled water and Styrofoam cups, implementing a recycling program in early 2009 that saved approximately seven tons of mixed-use paper from going to landfills, and making battery recycling available in all offices. Bodman’s Ann Arbor and Detroit offices recycle other materials, including plastic, glass, and aluminum containers. The offices also use energy efficient lighting fixtures with motion sensors that automatically turn off when a room is not in use. Other efforts are aimed at reducing paper by setting all high-speed printers to double-sided printing, electronically circulating internal reports that previously were printed, and offering clients the option to receive invoices electronically in PDF format. Although not new for 2009, Bodman’s Detroit headquarters in the former Hudson’s warehouse of the Ford Field complex is an outward sign of the firm’s commitment to sustainability by re-using a historic structure. The construction process incorporated numerous sustainable building practices including diverting 52 percent of all construction scrap from landfills through project-specific waste-hauler reporting requirements and an education program for on-site trades workers; floor tile fabricated from recycled tires and roofing materials; and wood veneers installed over an engineered backing of recycled wood. Bodman’s Environmental Law Practice Group works with businesses to obtain tax incentives and grants for sustainability improvements, often resulting in significant savings.
The Christman Company
www.christmanco.com
The Christman Co., a construction management firm, reached a milestone in 2009 when its 70th employee was accredited as an LEED (Leadership in Energy and Environmental Design) professional. Nearly two-thirds of Christman’s planning and operations staff - including project engineers, managers, executives, superintendents, and project planners - are now LEED accredited professionals. Christman has worked on nearly three dozen sustainable construction projects, the majority are either LEED registered (in progress) or certified, including the company’s national headquarters in downtown Lansing, Mich., that received the world’s first “Double Platinum” LEED certification, earning LEED Platinum status for both its commercial interiors, the core and shell. Now called The Christman Building, the structure (shell) is the historic landmark Mutual Building. Another LEED Certified project is the Mark Jefferson Science Complex at Eastern Michigan University, which will be complete in 2012, and Christman’s new West Michigan headquarters in Grand Rapids. “Christman’s LEED APs have displayed a commitment to strengthening their knowledge of sustainable construction, and we are proud of them all,” said Christman CEO Steven F. Roznowski, who also earned LEED AP status. “Our clients and business partners increasingly look to us to provide leadership in helping them achieve their green building goals, and engaging a fully LEED AP team from planning through execution makes realizing those goals much easier. Being green isn’t just something we do at Christman for show or to follow a trend - it’s something that translates into good business and it’s how we strive to operate on a daily basis.” With its roots stretching back to 1863 when Heinrich G. Christman started a contract excavating business in South Bend, Ind., with a team of draft horses, the company has regional offices in Grand Rapids, Livonia, Traverse City, Alexandria, Va. and Augusta, Ga. Its affiliated operations include Christman Capital Development Co., the real estate development division; and Christman Constructors, Inc., which provides excavation, demolition, concrete, carpentry, and other hands-on industrial construction services.
Contractors Building Supply
www.windowswindandsolar.com
When the Model Ts first hit the road, people and society weren’t ready for them. There weren’t gas stations on every corner, but the automotive industry grew and technology improved because the pioneers stuck with a good idea. In much the same way, Contract Building Supply Co-owner Allan O’Shea says that renewable energy technologies are a great idea and will rise above the current obstacles. “The challenge is huge to translate the world’s words and education into action,” he says. “We use a formula at CBS: Knowledge + Power = Success. Society has received a wake up call and now the question is, ‘What will we do with it?’ We need to walk the walk and not talk the talk.” One way of “walking the walk,” CBS is a distributor of the Windspire, a new type of compact vertical wind turbine, and installed one at its headquarters in Copemish, Mich., in January 2009. The vertical wind turbines can produce between 400 and 600 kilowatt-hours per month, which translates to a savings of $40 to $60 - or about 30 to 60 percent - of CBS’ typical monthly bill (the turbines produce more energy in the winter, when the weather is windier). Contract Building Supply undertook five other significant environmental initiatives in 2009 to reducing its carbon footprint by 65 metric tons annually (the equivalent of saving 150 barrels of oil or 7,360 gallons of gasoline). This included researching and developing renewable technologies, engaging in public outreach and education programs, training its dealer network, and working with school systems to demonstrate various renewable technologies. “We feel these savings are only the beginning and we will greatly exceed these numbers in 2010,” O’Shea says. On the R&D side, the company is creating hybrid solar and wind energy systems that effectively use both resources, providing more affordable costs to consumers. Public outreach and education is an important part of CBS’ mission to tell people about the benefits of sustainability. “CBS has a policy of speaking anywhere, at anytime, at no cost,” O’Shea says. “And our triple bottom line is geared at helping people, the planet and being profitable.” The company established and trained more than 30 dealers in Michigan, its educational outreach is enhanced by partnerships with Northern Michigan College, West Shore Community College, Petoskey College, Huron Valley ISD and many other schools where it has installed the Windspire and other renewable technologies. During 2007, Michigan spent a total of $27 billion to purchase energy from other states, O’Shea notes. It is a huge drain on the state’s economy. “Alternative energies not only are better for the environment, they also help keep dollars in our state,” he says. “Solar hot water is the most effective renewable energy people can employ yet we have no state funded support. Society needs to stay local and use the resources available in their own communities.”
Disposal and Recycling Technologies, Inc.
www.dart-inc.biz
Dedicated to providing its customers with the most reliable and cost effective way to dispose of waste, Disposal and Recycling Technologies, Inc. (DART) of Detroit also works to provide environmental solutions that meet stringent requirements. “Preserving our environment through effective waste management is a global responsibility,” says Erik Bomireto, president. “We apply our strengths to provide cutting edge disposal, recycling and wastewater treatment through technology and innovation.” Founded in 2005, DART’s environmental process includes the EnviroCHECK assessment program that provides clients with tools to implement green initiatives and economically sound waste management plans. Furthermore, DART clients can use its customized EnviroPLAN to implement a sustainable program with data tracking and reporting features. DART also started a subsidiary corporation, DART Alternative Energy, that has a patent-pending conversion model to effectively reduce landfill waste by 100 percent. The company expanded its current facility to recycle and dispose of containerized or bulk liquid beverage waste, outdated product, mislabeled or off-spec product from various industry sectors. The packaging from these products are recycled, while the alcohol and sugar based liquids are collected and converted into a fuel grade ethanol through DART’s advanced distillation process.
Duro-Last Roofing, Inc.
www.duro-last.com
![]()
|
One of the world’s largest manufacturers of prefabricated roofing systems, Duro-Last Roofing has built on its long-term commitment to improving its sustainable business practices during the past year. The Saginaw-based corporation began offering long-lasting membrane roofs in 1978 and discovered that most roof failures resulted from on-site workmanship issues rather than defective materials. Duro-Last developed a patented prefabrication system to construct the most difficult details under ideal factory conditions to lower on-site costs and improve installation quality thus saving time, labor and scrappage. Longer lasting roofs mean less roofing material ends up in landfills. “We were among the first roofing system manufacturers to institute a recycling program for roofs that have reached the ends of their lives,” says Jason P. Tunney, CEO. “Some examples of our green commitment is Duro-Last’s closed-loop manufacturing operation where all production scrap is ‘looped’ back into our products.” Scrap materials may be reused as roofing materials or for a commercial flooring system that’s made by Duro-Last’s sister company, Oscoda Plastics Inc., that recycles an average of 5 million to 7 million pounds of scrap annually. Another sister company, Plastatech Engineering Ltd., makes the Duro-Last roofing membrane and is in the process of installing more energy-efficient lighting, converting to more efficient alternating current motors, and is recycling about 500 gallons of waste oil each year. At one Duro-Last facility, efforts to eliminate waste reduced the number of landfill trips from a rate of one 40-yard dumpster that had to be emptied two to three times per week in 1996 to emptying the same dumpster only once or twice a month during the peak production season. This saves the cost of dumping fees while cutting the amount of refuse going to landfills. Duro-Last frequently communicates common sense approaches about green initiatives through its blog (www.duro-last.com/blog), with many posts about building materials, sustainability, cool roofing, LEED (a program of the U.S. Green Building Council), and photovoltaic systems. Most truly green or sustainable actions would make good business sense even if they weren’t green, Tunny notes. “In other words, an investment in green building technology is usually cost-justifiable.”
Dynamic Systems, Inc.
www.dynsys.com
With more than 20 years providing cleaning, vacuum cleaner rotation and customized cleaning supply distribution programs for its clients, Dynamic Systems held a ‘green-storming’ session to determine how to cut its carbon footprint, increase recycling and conserve water. “We looked at everything our company does that impacts the environment on a secondary level,” says David Mekled, president and CEO of the Dearborn Heights, Mich. company. “We created new electronic reports and recordkeeping procedures, but most of our work is conducted away from our office. For us, ‘going green’ in a measurable way meant adopting a much bigger field of vision.” Employees on all levels from sales to service were trained on better processes that protected the environment while serving more than 10,000 retail establishments nationwide. One such change was a major greening of Dynamic Services’ vacuum rotation program. When a vacuum at a client becomes inoperable, Dynamic Services sends a functioning unit to the store. The broken vacuum is repaired and entered back in to the pool of vacuums, waiting to be sent to the next store with a repair issue. “Our society was built on decades of taking and using our natural resources without thought to replenishment,” Mekled says. “When major environmental issues made the news, they were often associated with major corporations or years of damage. Many individuals or small business owners may not understand that they can impact the healing of the environment by changing one small thing.” The declining health of our environment didn’t happen overnight and there are no cookie-cutter solutions, he adds. Environmental education can be tailored to meet the various level of understanding in the community. By changing its business processes and service offerings, Dynamic Systems has spread an environmental-friendly philosophy beyond its employees to its customers.
Eastfield Laundry
www.eastfieldlaundry.com
Improving energy efficiency and decreasing his business’ environmental impact have been two of Jim Legato’s top goals since 2004 when he purchased Eastfield Laundry, a coin laundromat and commercial laundry company in Traverse City, Mich. All of Eastfield’s washers and dryers and lighting fixtures were replaced with more energy efficient units. All plastics are recycled at its coin and commercial laundry facilities and future plans include adding solar energy to help produce the hot water. Yet the biggest impact Eastfield Laundry had on the environment is switching to 100 percent natural cleaning products. In 2006, one of Legato’s employees, Ruth Smith, told him that all-natural detergents would reduce the amount of phosphates and other harmful chemicals that the laundromat disposed of in the city’s sewer system. When no 100 percent natural product could be found to meet their needs of cleaning efficiency and cost effectiveness, Legato supported Smith as she developed the phosphate- and dye-free, non-sudsing Selestial Soap (one of the 2010 Corp! Green Industry Innovators awardees) that is now exclusively used at Eastfield Laundry for all commercial jobs including the company’s diaper and equestrian laundry services. The product rinses cleanly from fabrics without leaving residue behind, making it perfect for use in Eastfield’s commercial business where linens for hotels and resorts are washed regularly.
eTitle Agency, Inc.
www.etitleagency.com
Dedicated to making home ownership more affordable by offering low-cost title fees, e-Title Agency of Troy experienced such rapid growth in a short period of time that it needed a new headquarters. Its executives were faced with the decision to either move out of state, construct a new building or renovate an existing building. They chose to undertake a multi-phase program, renovating an existing building with the benefits of reducing resource consumption, extending the useful life of the structure while not contributing to urban sprawl. The agency hired the Rossetti architectural firm that consciously reused existing ceiling grids and tiles, light fixtures and exterior doors, sidelights, plumbing fixtures, and directed the use of low volatile organic compound (VOC) paint. Seventy-five percent of the company’s office furniture was pre-owned and eTitle Agency built a 16,000-square-foot urban green space about its building with trees, shrubs, flowers and a walking path. “We opted to stay in Michigan, despite the state’s business tax,” says Linda Orlans, CEO, eTitle Agency. “We also realized that we could save costs and resources by being proactive with our eco-efficiency by starting an in-house conservation and recycle program.” Starting the “Green Team,” eTitle Agency has a group of employees that educates other staff members about sustainability issues and how to integrate environmentally friendly practices with everyday activities. “Our Green Team has us looking at new ways to sustain our natural resources for future generations and contribute to the quality of life of our employees and communities,” Orlans says. “From a business standpoint, many firms are facing the same challenge that we did - how to grow bigger while at the same time limiting and improving their eco-footprint. This can be done cost-effectively through a series of small incremental improvements.” The agency reduced the amount of waste sent to landfills by installing a permanent recycling center; going to a near paperless office, which saves over 2,500 boxes of paper a year; recycling cardboard, newspapers, magazines, plastic, glass and aluminum; plus replacing of all plastic silverware, plastic/paper cups and paper plates with real dishes, cups, glasses, and silverware.
Family & Cosmetic Dentistry
www.oaklandcountydentist.com
In addition providing patients with a beautiful smile, the partners of Family & Cosmetic Dentistry of Auburn Hills, Mich., wanted to give back to the community by building a new green office. In February 2009, the dental practice of Drs. Mike Tobola and Tracy Grindling opened a new building that was certified as meeting the Leadership in Energy and Environmental Design (LEED) requirements. The office is equipped with recycled bamboo floors, energy efficient lights with motion-activated sensors, the highest grade insulation possible, top-of-the-line energy efficient windows, zoned furnaces, low volatile organic compound (VOC) paints and stains, plus an in-house water filtration system. During the construction process, 95 percent of the waste was recycled. “It is our office’s goal to do our part to help maintain the environment,” Tobola explains. “We either re-use or recycle as much as possible. From using eco-friendly cleaning products to re-usable plates and utensils, we strive to waste as little as possible every single day.” The practice purchases recycled, eco-friendly paper products, cleaning supplies, and recycled printer ink cartridges. Patients are encouraged to pay over the phone or at the time of their appointment in an effort to reduce paper and carbon emissions. “We try to make a difference by showing our patients the simple tasks that have a huge impact,” Tobola says. “If every person cut back or put one more thing in the recycle bin, we could have a better world. Local businesses and communities need to encourage people to make a change. We need to show society that every effort helps.”
Food For Thought
www.foodforthought.net
Fifteen years ago, only about 3 percent of consumers were willing to pay premium prices for products that offered values beyond price, quality and convenience. Today, nearly 30 percent of consumers will pay a premium for a product or service that offers social, environmental or other more personal values, noted Timothy Fitzgerald Young, president of Food For Thought. Established in 1995 to raise organic and wild harvest gourmet specialty foods from the farms and forests of northern Michigan, Food For Thought is headquartered on an organic farm in the heart of the Sleeping Bear Dunes National Lakeshore. Its founder Young has been invited three times to Bon Appetite Magazine’s Wine and Spirits Festival in Chicago, participating with many of the Midwest’s best chefs. “Our company was founded on green and sustainable philosophies that have always been a part of our DNA,” Young says. “Therefore, unlike many companies, we are not redefining ourselves from a conventional business model to something more green. Every decision we make takes into consideration, not only on our economic bottom line, but also our social and environmental impact. This viewpoint at our inception led to our operation being based on an organic farm and housed in green built buildings. Our focus, as always, has been on bio-regional (local) foods that are either harvested in the wild, organic or Fair Trade.” Increased consumer demand for socio-environmental products is evidence of a quiet revolution happening across the planet, he says. The challenge for businesses is to promote and support this trend by making product and service decisions that are transparent to consumers. “Raising consumer awareness is the most important thing we can do to meet the challenges of sustainability,” Young says. “In all our communications - from our Web site and blog to our newsletters and print advertising - Food For Thought makes a concentrated effort to inform our customers about the impact of their decisions.” One of the company’s more visible projects is the annual event called Green Cuisine. Hosted on its farm, Food For Thought brings together the region’s best food and beverage artisans. Drawing more than 1,000 guests, the event is free to the public and offers an opportunity to sample the best of local delicacies.
Industrial Woodworking Corporation
www.industrialwoodworking.com
A major supplier to the health care and office furniture industries, Industrial Woodworking Corp. (IWC) of Zeeland, Mich., was recognized by the U.S. Environmental Protection Agency as a Green Power Partner in 2009. The EPA also included the company in its Green Supplier Network after it completed a technical review and mapped the value stream of its manufacturing processes. To fight global warming, IWC purchased Green-E certified renewable energy certificates to offset the estimated 400 tons of carbon dioxide generated by of its usage of electricity, natural gas, executive air travel and vehicles. “We recycle, source locally and offset our carbon emissions because we sincerely believe that our actions today have far-reaching implications for future generations,” noted Brad Davis, IWC’s chief executive officer. “The cornerstone of IWC’s business philosophy is an unyielding commitment to the environment.” Founded in 1995 as a supplier to the office furniture industry in western Michigan, IWC ships its products to every state and around the world. “We need to demand additional grant funding from government agencies to support corporate efforts to transition to renewable energy, including funds for installation of wind and solar equipment at manufacturing facilities,” Davis says. “There needs to be a relaxation of local building codes to allow companies to build wind and solar projects. And businesses need to request grant funds for training of existing employees for maintenance of renewable energy equipment.”
Newman Consulting Group, LLC
www.newmanconsultinggroup.us
Since the first “Oil Shock” of 1973, when the OPEC Oil Embargo created an energy crisis in the U.S., Europe and Japan, the Newman Consulting Group of Bloomfield, Mich., has provided clients with energy and natural resource conservation advice. During the past year, Newman Consulting worked with a number of architectural and construction firms to design and construct energy-conserving buildings, including office buildings, automotive and farm implement dealerships, warehouses, manufacturing plants, and an airplane hangar. It also was involved in residential building projects ranging from 1,200 square foot affordable homes for Habitat for Humanity to larger custom homes. “Our goal is to build environmentally sound buildings that are healthy to occupy, which reuse existing resources and conserve energy,” says James L. Newman, the group’s managing partner. “These buildings do not need to cost any more to build than those that are wasteful of natural resources as well as harmful to the environment.” The firm provides information, training and consulting services that encompass indoor environmental quality, energy conservation, the optimization of heating, ventilation and air conditioning (HVAC) systems, building renovations, and the requirements for designing green and sustainable buildings. “In the late 1980s, we became aware of the indoor air quality problems directly attributable to some of the energy conservation policies and procedures that had been put in place to reduce energy use,” Newman adds. “We have worked with engineering and building organizations to find the balance to maintain people’s health and conserve energy while decreasing the damage to our planet.” As the public became more aware of sustainability issues, Newman Consulting increased its speaking engagements to technical and non-technical groups, educational institutions, and business owners to help people understand what they can do to save energy, protect the environment, and save money with many simple and easy to do actions. On the Internet, the firm also posted a video on the American Recovery and Reinvestment Act of 2009 and a presentation on the Energy Policy Act of 2005 regarding what federal grants and programs are available to help businesses and individuals to conserve energy and save natural resources. Newman Consulting’s Web site is filled with information as well as links to many informational and government sites that help people and businesses get to this information. “There is a lot of talk about net zero energy buildings and renewable energy concepts such as solar, photovoltaic, wind, tides and true geothermal where the energy deep inside the earth is tapped, but it will be many years before they’ll make any real impact on our dependence on fossil fuels,” Newman says. “By concentrating on the shorter-term goals of greater energy efficiency in our existing buildings, we can start making that difference now.”
Priority Health
www.priorityhealth.com
A Michigan-based health insurance company, Priority Health has focused significant time and resources to ensure the organization helps the health of the environment. Among its recent accomplishments, the firm created a Green Team to encouraging other staff members to improve business practices, increase recycling, reduce energy demands, and use earth-friendly materials. It has made structural improvements by providing automated lighting, energy efficient vending and coffee services, live plants and facilitating “cool-air” strategies in its informational technology department. “We’ve approached being green from a business perspective,” says Kimberly K. Horn, president and CEO. “We continue to create new and innovative solutions to be an earth-friendly organization. We are so passionate about being green as an organization we have even federally registered the term, ‘Think Green.'” Priority Health has implemented various green strategies including: implementing paperless human resources processes (paychecks, benefit documents, etc.); recycling paper; using earth-friendly inks and papers for marketing materials; and purchasing green supplies, green furniture and finishes. It provides recycling services for its employees such as a bonus “pick-up” service for used batteries, lightbulbs and used computers. The company uses green products for its facilities functions; utilizing native landscaping to reduce water requirements and beet juice to de-ice the corporate campus instead of harmful salt byproducts. The results of Priority Health’s efforts have been successful, with the company recycling 185,135 pounds of paper, the equivalent of saving 1,572 trees; saving 647,970 gallons of water; reducing approximately 280 cubic yards of landfill waste; keeping 5,555 pounds of air pollution effluents out of the air; and saving 35,176 gallons of oil. “All of these changes reduce our energy requirements by $14,000 per year,” adds Horn. “The biggest challenge for our society is taking on green initiatives for the wrong reasons. When organizations challenge themselves to become green, they discover ways to be more efficient, reduce administrative costs and improve company morale. All while we make a positive impact on our environment.”
ReCellular, Inc.
www.recellular.com
The world’s largest recycler and reseller of used cellular phones and accessories, ReCellular of Dexter, Mich., has won numerous national and local awards for its comprehensive commitment to environmental protection. “In 1991, my brother Allan and I recognized an increasing number of Americans were using cell phones, discarding them frequently, and creating tons of solid waste even though most of the used cellular phones were still functional,” says Charles Newman, chairman and founder. “We saw the opportunity to start a new industry to refurbish, reuse and responsibly recycle discarded cell phones.” The firm partnered with the Cellular Telecommunications & Internet Association’s Wireless Foundation on the original “Donate a Phone” charitable recycling program, and has since developed long-standing relationships with key industry players such as Verizon Wireless, Motorola, Sprint, Best Buy and many others. All phones and accessories that cannot be reused are recycled; the company recycles thousands of tons of electronic scrap every year. ReCellular has donated millions of dollars to charities while tens of millions of phones are recycled or reused to customers in more than 40 countries.
Ricardo, Inc.
www.ricardo.com
With electrified and hybrid-electric vehicles a major part of automakers’ future lineups, United Kingdom-based supplier Ricardo, Inc., opened a new battery testing center at its Van Buren Township, Mich., facility in 2009. Ricardo’s 2,650-square-foot Battery Systems Development Center is the focal point of its design, analysis, simulation and integration of advanced high-power battery packs and their electronic management systems. Combined with the company’s expertise in the development of electronic controls, hybrid transmissions and vehicle systems, Ricardo can support a wide range of customers from cell suppliers to the other Tier 1 suppliers and OEMs. “Electrification of the vehicle is a critical element of automakers’ strategies for achieving the 35-mile-per-gallon CAFE regulations,” says Karina Morley, Ricardo global vice president of Controls and Electronics. “The Battery Systems Development Center is a state-of-the-art, benchmark facility that enables Ricardo to evaluate and optimize batteries throughout the development cycle, from the early stages through battery pack production and integration into the vehicle.” The battery center has a Virtual Vehicle Development Environment to fully simulate road, environmental and future vehicle designs in a safe, controlled and repeatable manner - allowing Ricardo to refine prototype battery packs and control systems before they are installed in a physical car. “We’re very proud of the fact that Ricardo is playing a role in positioning Michigan as the leader in electric vehicle technology development,” adds Ricardo North American President Kent Niederhofer. The company’s battery development expertise can be applied to non-automotive industries including agricultural equipment, military vehicles, plus medium- and heavy-duty on- and off-road vehicles, and any type of energy storage, such as ultra capacitors or batteries for stationary or other applications.
SchoolPictures.com
www.schoolpictures.com
![]()
|
In an effort to be “picture perfect” when it comes to conservation, SchoolPictures.com decided to renovate a pre-1950 structure, making it the first such building in Michigan to achieve the Leadership in Energy and Environmental Design (LEED) silver status. The company, known for taking more than 3 million student images and 10,000 class panoramic portraits, also changed its business practices to include a recycling and reuse program. “The past year truly defines our efforts to go green and limit our carbon footprint,” notes Skip Cerier, SchoolPictures.com president. “It goes without saying that ‘green’ is not just something we should do to market our company’s name or brand. It’s a way we should be living in our community simply because it’s the right thing to do.” Formerly the facility that housed Ave Maria College in Ypsilanti, Mich., SchoolPictures.com’s new headquarters includes green features such as: additional insulation to improve heating and cooling; low-wattage lighting and some motion-sensitive lighting; new base board heating and an increased number of zones for better efficiency; all new double thermal-pane windows; waterless urinals, which will save approximately 30,000 gallons of water per year; and all new recycled flooring products including non-PVC tile. During the renovation, the company recycled 80 percent of the 72 tons of debris that were removed from the site. Many materials were put back into the building including hundreds of glazed blocks to construct new walls and the original marble slab window sills. Counter tops were made from recycled beer bottles. “We also donated items from our building that were discarded by the previous occupant including library book shelving, wood doors and computer monitors, which are now being used by others in our community,” Cerier says. “We supplied a local library with $30,000 worth of shelving they needed and otherwise would have had to purchase. Now that we’re settled into our environmentally friendly facility, we continue to make every effort to be as green as possible. For example, we make it a habit to recycle paper and cardboard, and we use green cleaning products. We also participate in a program with DTE Energy to purchase our power solely from renewable energy sources.” Renewable energy offset programs allow companies to take advantage of renewable energy without having to purchase the hardware, such as a wind turbine, Cerier said.
Secure-24, Inc.
www.secure-24.com
![]()
|
A provider of managed hosting of critical information technology systems for industrial and governmental clients, Secure-24, Inc. built a new, state-of-the-art data center in Southfield, Mich., to reduce energy consumption while maintaining security and reliability. The $5 million center incorporates green design and industry-leading technologies. It joins Secure-24’s three other data centers in Michigan and Arizona to support clients across North America and around the world. Data centers typically consume a lot of power to cool computer servers and other equipment. “Every element of the new center - from locating it in a cooler climate, to cold aisle containment, raised floor design, server consolidation, private cloud computing, virtualization,
![]()
|
leading network, power and cooling technology and even sensor driven lighting - all contribute to improved efficiency and a lower CO2 footprint,” says Matthias Horch, CEO. By including environmental stewardship in its operating formula, the company has shown it can increase efficiency while simultaneously improving both business performance and the environment. “At Secure-24 we maintain an entrepreneurial small-company culture where individuals can make a difference and personal leadership and responsibility is rewarded,” Horch says. “We have a passionate team of professionals who work collaboratively to deliver real benefits to our customers, and to the communities where we work and live.” Over the next several years, Secure-24 expects the total investment in its Southfield center to exceed $10 million.
Tera Networks
www.teranetworks.com
Tera Networks of Northville, Mich., not only offers its clients data warehousing, hosting, managed services, disaster recovery and other information technology services, but through its Tera G initiative it can help small and medium size businesses green their IT infrastructures. With Tera G, the company identifies ways to reduce IT equipment power usage; offers paperless office solutions, such as electronic versions of employee manuals and other documents that can be readily accessed; and recycles used and broken equipment. Tera Networks removes and destroys hard drives from clients’ old equipment to prevent data loss and identity theft and sends the hard drive pieces and the remainder of the machine to an EPA-certified recycling company. Salvageable systems are refurbished and Tera Networks donates the equipment to nonprofit organizations. Tera Networks, a division of DataFactz, opened in the third quarter of 2009. Its parent company is also headquartered in Northville. DataFactz offers data warehousing and integration, business intelligence, IT consulting and IT outsourcing services to companies such as Con-way Freight, Darden Restaurants, Food Lion, Interstate Batteries, Ryder Systems, Volkswagen of America, and Walt Disney.
The Townsend Hotel
www.townsendhotel.com
Known for its luxurious appointments, elegance and classy ambiance, The Townsend Hotel of Birmingham, Mich. wants to be recognized as an environmental leader by openly sharing its practices with each and every guest. “By implementing and adhering to environmentally friendly practices, we are able to offer our customers better and healthier services and products, all the while keeping our utility and overhead costs down,” says Peter Wilde, managing director. “As a whole, the phrase going green can often make businesses and consumers think they will have to do-without or actually spend more money in order to stay up to par with environmental standards. In fact, this isn’t our experience at all. It truly is a win-win situation.” During the past year, the Townsend Hotel focused on the three Rs: Reduce, Reuse and Recycle. The hotel reduced water usage by providing a linen/towel reuse program to guests - replacing towels upon request - and installing low-flow shower heads, faucets and toilets. The hotel trimmed energy consumption by installing energy efficient light bulbs, insulating pipelines, conducting energy audits, and shutting down sections of hotel during slow times. The Townsend had cut solid waste - an estimated 70,000 plastic bottles, 40,000 plastic ice bags - by only ordering what is needed and implementing better practices. “We reduced our toxic waste by replacing cleaning and laundry chemicals with those that are less hazardous to the environment,” Wilde says. “We’re reusing by donating lightly used items like irons and hair dryers to charity, lost and unclaimed cell phones/phone chargers to Call to Protect and eyeglasses to charitable organizations.” Discarded terry cloth is used to make cleaning rags for staff. Lost, unclaimed books are added to the hotel library for employees. The hotel’s recycling program collects paper, magazines, plastic, cans, cartridges, batteries, etc. It prefers to purchase recycled or bio-degradable products in bulk from vendors that follow environmentally friendly practices. “By educating those around us on the importance and benefits of going green, we hope to encourage other businesses to join in the fight to combat global warming,” Wilde adds.
Turner Construction Company
www.turnerconstruction.com
![]() |
|
![]()
|
As part of its commitment to developing environmental sustainable practices Turner Construction Co. set a goal of trimming its absolute greenhouse gas emissions by 5 percent by 2011. Based in New York City with offices around the country, including Detroit, Turner is a member of the U.S. Environmental Protection Agency’s Climate Leaders Group. An industry-government partnership, the group works with companies to develop comprehensive climate change strategies. Partner companies commit to reducing their impact on the global environment by completing a corporate-wide inventory of their greenhouse gas emissions based on a quality management system, setting aggressive reduction goals, and annually reporting their progress to the EPA. “One of our major challenges has been overcoming the lack of reliable information on effective green building products, technologies, and building processes,” says Steven R. Berlage, president of Turner’s Michigan office. “There is a lack of an established recycling infrastructure that can help reduce recycling costs.” To counter the lack of information, Turner co-founded the United States Green Building Council (USGBC) in the 1990s and remains active in that organization both nationally and in Michigan. The company established new workplace habits such as turning the lights off in areas not being used,
![]()
|
encouraging employees to use public transportation instead of driving, and recycling paper. More than 1,200 Turner employees nationwide - more than any builder or architect in the country - are trained accredited professionals in the USGBC’s Leadership in Energy Efficient Design (LEED) program. This knowledge enabled Turner to refine its own construction practices to become more environmentally sensitive. For example, Turner has cut the amount of construction waste it sends to local landfills. Separate dumpsters on construction sites make it easy to sort materials for recycling. Using electronic, Web-based tracking methods, its workers record and document recycling efforts making it possible to know exactly where waste material is taken and for what recycling purpose. “Since 2005 in Michigan, over 28,000 tons or 88 percent of waste material has been recycled from Turner construction sites,” Berlage says. On LEED registered projects, Turner requires subcontractors to either obtain LEED Accredited Professional credentials or take an online LEED training course in order to increase their awareness of sustainable construction practices. That way, the entire construction team understands in advance what is required and how to proactively address green and LEED regulations on a project. “Turner’s initiative is similar to requiring a safety orientation and certification prior to beginning work on a construction site,” Berlage explains. “Many Michigan subcontractors that already have a LEED accredited professional on staff would automatically qualify. Those who do not can either pursue accreditation status through the USGBC, such as an Essentials of LEED Professional Accreditation course.”
Green Industry Innovators
ChemicoMays, LLC
www.chemicomays.com
![]()
|
During the past year, the Chesterfield, Mich.-based ChemicoMays implemented a wastewater recycling system to cut its daily city water usage by 30 to 50 percent, resulting in significant financial savings and helping the environment. “One of our main processes requires 3,500 gallons of city water per day and historically we treated the wastewater and send it all to drain,” notes Leon C. Richardson, president and CEO. “The new process allows us to recycle up to half the treated water back into the process, eliminating the use of 437,000 gallons of city water per year.” ChemicoMays was formed in 2006 as a 50/50 joint venture between Mays Chemical Co. and Chemico Systems, an automotive supplier that does industrial paint stripping. It has taken automotive chemical management skills and applied them to other clients in the government, biotechnology industry and academia. For example, the Lansing, Mich. school district hired ChemicoMays to supply its chemical needs for science laboratories, fertilizer for football fields, and swimming pool chlorine. ChemicoMays helped trim the schools’ costs by 5 percent while reducing its environmental footprint. “The biggest challenge society faces in becoming more environmentally friendly is mental,” Richardson says. “There are so many little things that everyone of us can do to help the environment, the things your mom told you such as turn off the lights when you leave the room; fix the leaky faucet; and walk or bike to the corner store.” The company educates and mentors its employees, customers and suppliers on what they can do to help reach environmental objectives.
ecostore USA
www.ecostoreusa.com
The idea for ecostore USA came partly from the desire of Lyne Appel Downing, the company’s vice president of operations, who didn’t want to use “Nasty Chemicals” all over her house. About three years ago when searching for an eco-minded, health-related business opportunity she discovered a New Zealand-based manufacturer of toxic-free household, baby and personal care products. ecostore NZ sold household cleaning products using biodegradable plant-based ingredients, eliminating toxic chemicals that could pollute waterways. Downing contacted its founders, Malcolm and Melanie Rands, and became the U.S. distributor. “I was impressed with the products and with the notion that they were already a known brand-name in New Zealand,” Downing said. Based in West Bloomfield, Mich., ecostore USA opened for business in 2008 by launching its Web site. Using a blog to reach out to moms who were interested in green products, the startup business became successful within six months. Facebook, Twitter and YouTube were other important marketing venues. By March 2009 it was distributing its products through the Meijer superstore chain. “We started to target our market to mothers like myself who wanted a safe, green environment for their families,” Downing says. “We realized that moms talk, share information about brands and products at the bus stop, through text messaging, and on the social networking sites. People in general would be more comfortable about greening up, if they began with little steps that are relevant to their own lifestyle. It can be as simple as not taking a long hot shower, or not running water while brushing their teeth, or dialing down the thermostat and putting on an extra sweater. Little steps help make the bigger ones happen.” ecostore USA offers more than 100 products that meet stringent environmental and sustainability standards, meaning that every formulation must be good for the user and for the planet. “We were very careful about selecting the retail store to sell our green household product line. We chose Grand Rapids, Mich.-based Meijer as ecostore USA’s first retail outlet because it has a sense of local community and its product values fit ecostore’s mission to target the middle-range supermarket shopper rather than someone who goes to a higher-end or a mom-and-pop store.” When ecostore hired college students, who became known as Ecovisors, to provide information to prospective Meijer customers; sales tripled. The company also offered coupons to accelerate sales. ecostore USA baby projects will be available at Meijer in early 2010. Recently the company partnered with the flagship store of Duane Reade, a New York City pharmacy, with plans to expand the line to all of the pharmacy’s 250 stores by early 2010. “We recently found an American manufacturing company with the right fit for ecostore USA, so we didn’t need to strictly import products from New Zealand for distribution.” Three of its product manufacturers are located in the U.S., with one of those in Michigan.
Eden Environments
www.EdenEnvironments.com
Western Michigan’s first sustainable design center, Eden Environments of Grand Rapids, assists clients in creating new or remodeled homes and businesses with architectural, interior and landscapes that use sustainable building materials, finishes, and furnishings. “We face major economic issues, being green is often considered too costly, however most sustainable products are right in line with traditional products’ initial costs,” says Denise Hopkins, architect and owner. “Typically businesses only look at the initial costs when evaluating products or systems. Even if you don’t believe in global warming, the statistics show that we are wasteful and destroying our environment at a rate from which it cannot fully recover or continue to support life as we know it.” Hopkins is a licensed architect and a LEED accredited professional with nearly 20 years of experience. To educate people about the benefits of living a green lifestyle that is good for both the personal and global environments, Eden held cleaning, cooking and even children’s classes in the past year. “In our healthy cleaning classes, Eden made it easy for individuals to change from toxic cleaning products to healthy organic cleaners that are good for us, our families, and our water systems,” she says. “Other sustainable selections include paint, carpet, furniture, fabric, clothing, and more.” In partnership with CompRenew, a local nonprofit electronics recycler, Eden educated people on how they can take their broken and unwanted electronics so they can be repurposed or recycled and kept out of landfills. Also, the West Michigan Environmental Action Council, Coca Cola, and the City of Grand Rapids sponsored two rain barrel workshops at Eden where participants learned how the barrels can reduce storm water discharges into sewers and provide water for gardens. In the cooking classes, participants learned about the benefits of eating local organic food. Eden’s Abrakadoodle art classes taught children how they can personally make a difference in the world. “Society today faces many challenges in becoming more green,” Hopkins says. “We make a statement in every action that we take from recycling to using our own grocery bags to buying renewable energy. And each individual’s actions have an impact, especially in spreading the word and the importance to our colleagues, family, and friends.” Eden’s goal is to be a role model and practice what it preaches by pushing for better methods and products, and reject systems and materials that harm people and the environment.
Erie Architectural Products Inc.
www.erieap.com
A specialist in curtain walls, window walls, entrances, storefronts and skylight systems, Erie Architectural Products has its own in-house LEED accredited professionals who help clients meet stringent energy codes and identify the most appropriate curtain wall system for any construction project including those that earn LEED credits. Through strategic alliances with its partners, Erie Architectural Products can introduce Building Integrated Photovoltaic Panels into a building facade to help meet energy codes. Based in Blenheim, Ont., Canada, in 2008, EAP added a new facility in Novi, Mich. that is home to Erie Architectural Products USA Inc. and Erie and Associates Engineering, Inc. “We are very committed to green, sustainable and environmentally sound practices and we have several products that allow our customers to meet their LEED certification requirements,” says Tim Thomas, sales manager of Erie Architectural Products USA. “Along with our suppliers, we have developed high performance curtain wall systems, glazing, sunshades and light shelves that not only improve the energy performance of a building but also increase the comfort level of its tenants. Our plan is to expand our fabrication capacity in the U.S. in 2010 and hopefully that facility will be right here in Michigan.” It has worked on several large curtainwall projects in Michigan including most recently, Henry Ford Hospital of West Bloomfield.
Faurecia
www.Faurecia.com
With a U.S. federal mandate to boost fuel-economy to 35 miles per gallon by 2020 and more consumers looking to buy eco-friendly vehicles, the automotive industry is implementing new technologies to meet the challenge. Faurecia, a global automotive supplier with its North American headquarters in Auburn Hills, Mich., unveiled the “Light Attitude” concept a little more than a year ago as an answer to that challenge. Using renewable and recyclable materials, the Light Attitude concept cut vehicle weight by as much as 130 pounds, thereby improving gas mileage, while trimming carbon and nitrogen emissions and making vehicles easier to recycle at the end of their lives. “The development of Faurecia’s Light Attitude concept is our most significant initiative in the last 12 months to help protect the environment and limit not only our footprint, but also the footprint of people around the world,” says Michael Heneka, president, Faurecia North America. “Light Attitude is a collection of game-changing innovations that challenge the form and function of today’s vehicles. These innovations could be adopted by automakers to significantly reduce the weight of tomorrow’s vehicles.” For the next generation of vehicles, Faurecia’s engineers are working to cut component weight by up to 30 percent while incorporating premium-level comfort and safety features. One such development is its Sustainable Comfort seating technology. “In the latest version we have reduced the depth of the seat back for the driver and front passenger, freeing up considerable space in the vehicle cabin,” Heneka says. “At the same time, the seat is more comfortable than many conventional systems because Faurecia uses molded biometrics: the back and cushion are molded to the human form. The same cushioning that provides sports shoes with their comfort and flexibility replaces traditional foam in Sustainable Comfort seats.” Attractively designed, the seat’s composite back shell can be finished with Faurecia’s Ligneos wood grain that incorporates natural wood fibers. Faurecia supplies components to 16 of the 20 most fuel-efficient vehicles in the world, based on automakers’ published mileage reports. Faurecia also progressively implemented environmental management systems, based on the ISO 14001 international standard, to 102 of its sites and offers training and awareness of environmental protection to all employees.
GiftZip.com
www.giftzip.com
Having started in June 2009, GiftZip.com is helping to curtail the wasteful plastic gift card market by making it easier for consumers to purchase electronically delivered cards - basically getting a gift card without the physical card. “Seventy-five million pounds of toxic, carcinogenic PVC (polyvinyl chloride plastics) goes into landfills in the U.S. each year because somewhere along the line we decided to print these electronic codes on plastic cards,” says company founder Sam Hogg. “The plastic gift card is not only harmful in disposal, but the manufacture, distribution, and storage of the cards has a tremendous energy and carbon footprint.” Based in East Lansing, Mich., GiftZip.com provides consumers access to hundreds of retailers’ instant, e-mail gift cards. By being able to purchase gift cards online, it saves consumers time and energy, without sacrificing their shopping experiences. The electronic gift card arrives in the recipient’s e-mail inbox and can be redeemed in-store or online. Hogg originated the business plan for GiftZip.com while attending a sustainable supply chain course at Michigan State University. He realized that in the shorter term, companies that don’t evaluate efficiency and sustainability are wasteful and ultimately less competitive because waste always has costs associated with it. Stores ranging from Target to niche retailers such as Culinary Teas have signed up with GiftZip.com. Merchants pay the online company a percentage of sales or through the exposure of alerting customers to GiftZip’s existence. “Consumers need to be able to distinguish between price and total cost,” Hogg notes. “The business world is consumer-driven, so as long as the consumer is only worried about price, businesses will make decisions to deliver on that. It is much easier to operate on a pull model versus push - it is much easier to respond to markets than create them. If the consumer wants more sustainable products, businesses will chase them.”
Great Lakes Recycling
www.go-glr.com
Founded in 1927, Great Lakes Recycling is a full-service recycling processor offering on-site retrieval of paper, metal, electronics, plastics and foam through its commercial division, as well as office paper recycling through its corporate office recycling program. Headquartered in Roseville, Mich., the company recently added two new facilities in Michigan -in Flint Township to process paper, cardboard and non-ferrous metals; and a $12 million, state-of-the-art Huron Township facility. These facilities allow for more items to be recycled, cutting waste going to landfills. To help increase recycling awareness, GLR offers education programs. “What sets Great Lakes Recycling apart from others in the industry is our passion and commitment in educating people on the importance of recycling and the impact it has on the environment,” says Sandy Rosen, co-owner. “Our newest facilities in Huron Township and New York are specifically designed with the education of recycling in mind. We offer tours and make education materials available for schools, groups, organizations and the general public. The mezzanine watch area over the plant gives everyone the opportunity to see the recycling process as it moves material along conveyor belts, sorts according to product, and produces bales for shipping to mills to create new products. Recycling behavior is voluntary. The more you know-the better decision making you will have.” The company has a fleet of more than 200 tractors, trailers, and roll-off containers and a 24-hour, 7-day a week dispatch service. Its 15-acre Roseville facility has two public drop-offs that accepts any range of metal, plastic and paper, including a cardboard sort line and numerous secondary sort stations for high-grade papers. It processes more than 175,000 tons a year. For the second quarter of 2010, GLR is launching an “In the Bin” advertising program with radio and TV spots, billboard and truck “wrap” advertisements, plus Web ads to promote recycling in general.
Heat Transfer International
www.heatxfer.com
One of the banes of raising livestock is what to do with the accumulated animal waste. One solution has been offered by the alternative energy company Heat Transfer International which partnered with The Right Place of Grand Rapids to open the world’s first biomass power plant on a Michigan farm on Oct. 23, 2009. Headquartered in Kentwood, Mich., Heat Transfer designs biomass gasification and electric power generation systems that convert solid and semi-solid biomass - such as animal manures, agricultural waste, solid waste from landfills, wastewater treatment sludges, sewer sludges, and hazardous waste material - into a combustible “syngas” that can fuel power generators, dryers, heaters and cooling equipment. The gas and electricity produced is considered “carbon neutral” and thus environmentally green. Housed at the 40-acre Semantic Farm Feeds, just south of Howard City, Mich., the Heat Transfer plant, powered by a Hot Air turbine, will convert manure from 1.5 million turkeys into electrical energy. All residual waste heat will be used to create steam to soften the corn that is used to make pig and turkey feed. “The biggest challenge for alternative energy producers is the wild fluctuations of conventional natural gas and electricity pricing,” says Dave Prouty, president of Heat Transfer. “The prices are not high enough for sustained periods of time to cause the majority of people to want to invest and change from easy-to-use fossil fuels. Also currently, banks are so risk adverse given all the bad investments of the past that they are not willing to fund alternative energy projects.” As an alternative energy technology company, Heat Transfer is continuously working to improve the reliability of its systems and reduce costs to be able to compete head to head with conventional fossil fuels.
Interstate Traveler Company, LLC
www.interstatetraveler.us
The way to eliminate congestion on America’s highways - which would help reduce air pollution, not to mention saving people “lost time” due to traffic jams - may be a re-visioning of the municipal infrastructure. Interstate Traveler Co. of Whitmore Lake, Mich., proposes building a magnetic levitation (maglev) light rail system that also acts as a conduit cluster for common municipal utilities for water, natural gas, electric, fiber optic, high-temperature superconducting cable, liquid or gaseous hydrogen, and pressurized liquefied waste. “All nations face the same infrastructure dilemmas; that is why the Interstate Traveler is a truly global enterprise for a truly global need,” says Jay C. Wilber, CEO. “Directly servicing the ever growing populations of the world with reliable and quickly installed utility conduits for electricity, potable water, fluid waste, liquid and vapor based fuels, and public transportation is our mission. The utility clustering principle being exploited by the benefits of mass production using materials that guarantee hundreds of years of service, is the ultimate investment of both public bonds and private venture capital. Steel tubing is very quickly formed to the quantity that will allow miles of track to be installed per month, and even miles of track to be installed in a single day with the back log of pre-fabricated, modular, mass-produced sections.” The Interstate Traveler Hydrogen Super Highway - also called HyRail - would be built along the right of way of existing interstates. The HyRail could be accessed by Traveler Stations built within the land-locked real estate of the clover leaf interchanges, providing maximum ease of access for people who live anywhere near the Interstate Highway. “The HyRail public transit network will enable millions of people in the future to utilize on-demand publicly owned transit vehicles that share the same maglev rail with privately owned transit vehicles,” says Wilber. “Essentially the HyRail represents the addition of new lanes of transportation traffic on existing rights of way.” The railway could be elevated above the ground, providing for a green corridor underneath for carbon sequestering. The HyRail would have passenger and freight trains, as well as special passenger/car carriers.
Kinetic Wave Power, LLC
www.kineticwavepower.com
![]()
|
The 2009 grand prize winner in the Great Lakes Entrepreneur’s Quest awards’ emerging company category, Kinetic Wave Power of Midland, Mich. developed an innovative hydroelectric technology that taps the power of ocean waves. Called the PowerGin, Kinetic Wave Power’s generator captures more of the energy contained in a wave than any other method. It combines overtopping wave technology, making use of the wave’s vertical (rise and fall) energy, with a wave ramp to transform horizontal kinetic energy into a useable form. Using both vertical and horizontal wave energy allows much greater energy conversion efficiency than existing wave energy technologies that only use the vertical component. The PowerGin can operate in lower and variable wave areas - such as southern California and the Eastern Seaboard - where other wave energy converters do not function. “Our technology has the potential to deliver electricity that is cost competitive with coal and uses the ocean as a free, abundant and renewable green energy
![]()
|
source,” notes James A. Sack, Kinetic Wave Power vice president of technology. “One of the largest untapped natural energy supply options is the energy contained in ocean waves. As the sun heats the air differentially it creates wind. The wind blows across the ocean to create waves. The resulting ocean waves are about 25 times more energy dense than the original solar energy that created them. The ocean serves as a giant solar collector and is able to concentrate this energy, package it in a wave front and deliver it to nearly every major population center in the world.” It is estimated that if 0.2 percent of the ocean’s energy could be tapped, it could power the world five times over. “Our society needs to adjust their view of renewable energy to include the ocean as a key source of energy and begin to explore ways to harvest this natural, green, and renewable energy source,” Sack says. “A reliable and robust electrical system in any country requires a balanced and diversified portfolio of energy supply options.” Some European countries are already sourcing 20 percent of their electrical needs from renewable energy sources. Kinetic Wave Power continues to put a significant focus on educating America on the energy potential contained in the ocean and commercializing its new highly efficient electrical generating technology. “We ask you, Michigan, to ‘Catch The Wave’ and support Kinetic Wave Power in promoting green technology,” says Sack.
LeanLogistics, Inc.
www.leanlogistics.com
One problem facing trucking and freight carriers is how to eliminate empty miles - the times when an empty trailer needs to be hauled back to the terminal after making the last delivery. LeanLogistics of Holland, Mich., a supply chain service and transportation technology provider, recently launched GreenLanes, a freight optimization program designed to reduce empty miles thereby trimming fuel consumption, greenhouse gases, and air pollutant emissions. Normal freight consolidation programs optimize individual shipments, but few organizations have the network volume to address lane efficiency, with the ability to optimize multiple shipper demands across multiple carrier capacities. “The current economic market is challenging most organizations and they are looking to green their supply chains,” says Dan Dershem, CEO and president. GreenLanes goes well beyond traditional freight consolidation, he says, by using an engineered solution that benchmarks network-wide coverage, rates, and performance so shippers obtain the best possible service and value from carriers, while carriers operate at optimum capacity. In most cases there is a reduction of empty miles from 15 to 20 percent to 3 to 5 percent, benefiting both shippers and carriers. “We are able to identify, even predict, opportunities for lane and load optimization, making the best use of available assets, which in turn reduces the carbon footprint,” Dershem continues. “This is a sustainable program for shippers and carriers.” GreenLanes delivers financial and environmental benefits to shippers and carriers by allowing transportation managers to determine opportunities for round trips, continuous moves and Fractional Dedicated Truckload. LeanLogistics also is a SmartWaySM partner, a collaboration between the U.S. EPA and the freight industry to increase energy efficiency and significantly reduce greenhouse gases and air pollution.
Meadowlark Builders
www.meadowlarkbuilders.com
Building and remodeling homes to use up to 10 times less energy than an identical conventionally-built home, Meadowlark Builders of Ann Arbor, Mich. is a full service design and construction firm that combines knowledge of high-performance systems with an artisan’s touch. “We incorporate local commerce, community service, and recycling into our everyday practice,” notes Doug Selby, who co-founded the firm in 2004 with Kirk Brandon. “We innovate with our building methods to strive for the apex of sustainability - homes that make more energy than they use and have a net positive effect on the environment.” The company is in the startup phase for Meadowlark Energy Solutions, a subsidiary that will perform energy retrofits to make homes more energy efficient, comfortable and healthy. “Historically Americans have preferred a short-term gain over long-term efficiency and durability,” Selby says. “We aim to raise people’s awareness of the benefits of long-term thinking.”
The Night Move
www.thenightmove.com
Shuttling weekend party-goers to and from the suburbs to Detroit’s swinging nightclubs to practice some “Night Moves,” as Rock Hall of Famer Bob Seger might say, The Night Move is the region’s first green bus line, operating two shuttle buses running on b20 bio-diesel fuel supplied by a Detroit-area company, Clean Emission Fluids. The bus company has partnered with area businesses for special event tours. “Our entire business has been built on a green foundation,” says Chris Ramos, owner of the Ferndale, Mich.-based company. “Through spreading the word about our business, we’ve found that it is equally important to spread the word about taking initiatives to live, work and be green. Strategic partnerships with a ‘green’ cab company, Recycle Here Detroit, among others, have helped to strengthen our commitment to eco-friendly practices as well as expand the outreach of our voice in relation to eco-conscious living.”
Selestial Soap, LLC
www.selestialsoap.com
Parent Tested Parent Approved Media picked Selestial Soap of Traverse City, Mich., as its 2009 Go-Green Product Award Winner for its high quality, functionality, style and environmental friendliness. “We developed Selestial Soap after discovering that the vast majority of ‘natural’ laundry products on the market were not 100 percent natural, contain unnecessary ingredients, weren’t effective cleaners, and/or were priced so high that many consumers couldn’t fit them into their budgets,” says Ruth Smith, who co-owns the company with Jim Legato of Traverse City. With its phosphate-free, non-sudsing formulation, Selestial Soap can be used in high efficiency washers. It rinses cleanly from fabrics and the machine’s insides without leaving residue behind. Fabrics washed in Selestial Soap can help prevent irritation for people with skin sensitivity issues. The company also introduced two new products in 2009 to reduce the footprint of its product line, including concentrated 16-ounce refill bottles and Outdoor Extreme Laundry Soap. By adding water, the refills can replenish an empty Selestial Soap 100-ounce bottle or can be used in its concentrated formulation. The refill uses less packaging, so it is both more economical and reduces the impact on the environment. The Outdoor Extreme Laundry Soap was formulated to meet the specific needs of hunting, tactical, and athletic clothing where scent, UV brighteners and residue are an issue. Only one capful of the super-concentrated detergent is needed per load so a 16-ounce bottle should wash about 50 loads in a standard machine or 100 loads in a high efficiency machine. “All of our products are 100 percent natural and do not contain unnecessary fillers or surfactants that can harm the fabrics being washed and the environment,” Smith notes. “In the cleaning category, we believe that the biggest challenge is finding products that are truly 100 percent safe for the environment because there aren’t any regulations on the use of the words ‘green’ or ‘natural’ for cleaners.” She adds that consumers “are paying premium prices for products that they believe in, but that are really not much different than traditional detergents.”
Studio 5
www.studio5inc.com
![]() |
|
![]()
|
An innovator when it comes to designing sustainable architectures, interiors and landscapes, Studio 5 of Birmingham, Mich., looks at how building materials will be used from cradle to grave. “LED (light emitting diode) and high efficient lighting are the only specifications we use for all our building environments,” says architect and CEO Holly Kaiser. “We made client education a major component of our studios. We have classes for clients, homeowners, design professionals, builders and inspectors geared toward their particular interest in sustainable design.” Although society measures success by what people have - the more the better - the architectural firm tries to show and educate its clients on ways to save their money while maintaining their quality of life through innovative design and use of the right sustainable materials for the job at hand. “Until the people see that they can live fully satisfying lives with really quite little, many will unfortunately continue to collect things to satisfy their desires,” she says.
TEAM Industries, Inc.
www.teamindustries.com
Perhaps in the future consumers will feel less guilty about using Styrofoam plates and cups for their picnics if they know that the material can be recycled and used in insulation building materials like those being produced by TEAM Industries. A supplier of foam insulation and packing products with facilities in Kentwood, Mich., TEAM Industries began recycling all of its expanded polystyrene (EPS) foam three years ago. This reduced its landfill waste by more than 80 percent. It now uses recycled EPS - such as from foam coffee cups - in some of its products such as the R-Control structural insulated panels (SIPs). The panels use foam insulation that is laminated between sheets of structural sheathing. This composite sandwich forms a strong structural panel for building walls, roofs and floors. “As a construction methodology, our R-Control brand SIPs contribute to a smaller carbon footprint primarily through reduced energy consumption due to the relatively higher R-Values,” notes CEO Michael Waldschlager. “There is no off-gassing from our product because SIPs do not contain any ozone depleting blowing agents such as CFC, HCFC or HFC. We use recyclable materials to manufacture R-Control SIPs, helping to significantly reduce job site waste when compared to traditional construction methods.” For those companies seeking a Leadership in Energy and Environmental Design (LEED) designation, the U.S. Green Building Council awards points for builders using TEAM Industries’ R-Control SIPs. “Other LEED recognition potentials include local and regional materials and rapidly renewable materials,” Waldschlager says. “We are aggressively educating the architectural and design community as well as owners regarding the sustainable advantages of building with R-Control SIPs. It is critically important that consideration be given to the life cycle cost/benefit of building with SIPs.” Although the material costs of SIPs may be more than traditional stick frame construction, typical installation time and labor costs are halved. Building owners should see energy costs reduced by 40 to 50 percent. The insulated panels can be custom made to meet exact specifications and drawings. When one considers all costs and related benefits, it is a sound economical and environmental decision to build with SIPs, Waldschlager added.
Thetford Corporation
www.thetford.com
![]()
|
“Green” is the buzzword in 2009, but Thetford Corp. of Ann Arbor, Mich. is one of the few companies to develop and produce green products for those consumers truly in tune with nature - recreation vehicle owners and boaters. Thetford has introduced a full line of green deodorants and green cleaners that have been certified by the U.S. Environmental Protection Agency and recognized by the BoatU.S. Foundation for the outdoor recreational market. The EPA named five of Thetford’s new RV and eight marine products as Design for the Environment (DfE), which is the new standard for “green” products in the United States. Additionally, the BoatU.S. Foundation awarded Thetford’s Boat Wash a “Staff Pick” as being the best all-around green product for cleaning, performance, toxicity, biodegradability and cost. DfE is a partnership program by the National Sanitation Foundation and EPA that recognizes companies that design for the environment and human health by using only safe chemicals. “Because Thetford’s products are used outdoors on RVs and boats, the EPA held our products to a standard higher than household products,” says Mary Burrows, Thetford manager of chemical development. “The new formulations were thoroughly tested in-house and with RVers. We were able to maintain the same exceptional product performances, all within DfE-recognized formulations. Thetford also introduced a full line of EcoLogo certified holding tank deodorants under the EcoSmart brand.” EcoLogo is North America’s oldest, most-recognized and respected environmental standard and certification agency. Thetford passed all requirements for its entire EcoSmart line. “As a manufacturer of consumer products for the outdoor recreational industry, we will strive to continue to develop and introduce products that are powerful performers and are third party certified and recognized as green,” Burrows says. “We will be introducing more DfE recognized products this year and in the future. We will also educate the consumer on what is truly a green product versus one that just claims to be green, so the consumer can be certain the product they are using is truly a green product.”
The Whole Brain Group
www.thewholebraingroup.com
The Whole Brain Group LLC of Ann Arbor, Mich. is a Web-application development company that has worked with the city’s chamber of commerce and the University of Michigan on ways to cut paper usage. For the Ann Arbor Chamber of Commerce, The Whole Brain Group developed an iPhone application that eliminated the paper version of the member-to-member discount directory, which often became outdated soon after printing. In the past, chamber members had a difficult time updating their chamber directory discounts. Now available online, the directory’s updates including discounts are automatically sent to chamber members via the iPhone application each week. “The iPhone application increases chamber members’ visibility,” notes Marisa Smith, Whole Brain Group president. “Anyone may download the free application from the MAC iStore to their iPhone and gain access to hundreds of businesses’ information such as names, descriptions, locations and Google mapping, phone numbers, e-mail addresses, discount offers and contact names.” Future iPhone versions should include new services such as advertising space, boosting the chamber’s revenue. The application has greened up the chamber by reducing paperwork, the use of ink, and mostly cutting the amount of time people spend in tracking and organizing the data. For U-M, the firm recently completed development of a Web-based system to allow the president’s office to more efficiently track nominations for honorary degrees typically awarded at commencement ceremonies. Traditionally the nomination process involved a lot of paperwork and/or confusing strings of e-mailed applications.
Green Organizations
Cass Community Social Services
www.casscommunity.org
Founded during the Great Depression, Cass Community Social Services has more than seven decades of experience of fighting poverty and helping the needy in Detroit. In late 2007, the organization began looking at ways of reducing its environmental footprint with recycling and conservation programs linked to job training and employment placement. CCSS’s most recent initiative is equipping its new gym with 10 stationary exercise bikes that can be pedaled to produce energy. It is estimated that the bikes will create enough energy in a year to light 36 apartments for a month. Simultaneously, the gym improves the health of homeless men, women and children, while generating power that reduces the agency’s carbon footprint. “Perhaps one of the more pressing issues related to going green is making it affordable on the front side,” says Rev. Faith Fowler, CCSS executive director. “There are small steps people and institutions can take to be better stewards of the environment, but significant changes such as furnace replacement, solar panels, or wind turbines require considerable investments which are out of reach for low-income people/organizations.” The agency helps people by providing for basic needs such as affordable housing, promoting self reliance and encouraging community inclusion and improvement. One of CCSS’s businesses is a document destruction (shredding) program where developmentally disabled adults sort, shred and bale paper. Most of it contains sensitive information so the highest security measures are used to ensure and document the chain-of-custody. The program’s regular customers include physicians, lawyers and other offices. The organization is exploring how it can turn the shredded paper into insulation for low income homeowners. If feasible, the insulation program would serve multiple purposes by employing adults with developmental disabilities, recycling paper otherwise headed for a landfill and permanently reducing the energy consumption/heating bills for poor people. Another business operation employs formerly homeless men to collect more than 5,000 tires that were illegally dumped on vacant lots in Detroit. At no cost to the city, the program converted the tires into mud mats with sales of more than 2,000 by June 2009. Finally, CCSS is negotiating a contract with a local business to assemble solar panels at a third of the normal cost.
Central Michigan University
www.cmich.edu
Central Michigan University made several significant strides during the past year to cut energy consumption by 20 percent, water usage by 6 percent, increase recycling by 30 percent, and reduce its carbon footprint 10 percent by implementing a campus-wide sustainability plan. Designed to foster a culture of conservation and sustainability, the action plan impacts everything from facilities management and custodial operations to campus dining and information technology programs. The university will track its progress on meeting specific goals and objectives to be reached by June 30, 2013. “We are constantly faced with the challenge of meeting the needs of a growing human population with the finite, limited resources of our small planet,” says Kathleen Wilbur, interim university president. CMU’s commitment to reduce energy consumption includes refurbishing a steam boiler that will be powered by renewable biomass fuel; install new ceiling fans in its Indoor Athletic Complex that should lower heating costs by 25 percent; replace lights with energy efficient fixtures; and sponsoring an electric competition between five residence halls that resulted in a 9 percent reduction in energy consumption. To improve campus storm water management, a vegetative roof was installed on half of the Education and Human Services Building, which also provided additional benefits such as reducing air conditioning costs by lowering rooftop temperatures, providing sound insulation, and extending roof life by shielding the membrane subsurface from ultraviolet rays. Plans to reduce water consumption will be tackled by replacing water lines and installing low flow fixtures in residential halls; and installing 0.5 gallon per minute aerators on 4,500 faucets across campus. To increase recycling from a base level of 455.5 tons to nearly 600 tons by 2013, eight recycling dumpsters were added around campus along with 500 paper recycling containers, 250 bottle/can recycling containers, 1,850 individual containers in residential halls; and making curbside recycling available for all apartment complex residents. Other actions included holding a recycling competition between residence halls during the fall semester that collected 20 total tons; participating in the national “Recyclemania” competition during the spring semester. CMU encourages students, faculty and staff members to use mass transportation, car pooling, and bicycling by adding 50 bike racks, six new bus shelters, and installing bike lanes on campus roads. To trim the university’s carbon footprint, many campus vehicles were converted to run on B20 bio-diesel fuel; geothermal energy will be used to heat and cool CMU’s Biological Station’s Academic Center on Beaver Island; and the campus sustainability plan calls for implementing LEED practices for design and operations on all campus projects and buildings; and achieve LEED certification on all new buildings, additions and major renovations.
Clean Energy Coalition
www.cec-mi.org
In 2009, the U.S. Department of Energy awarded the Ypsilanti-based Clean Energy Coalition a $15 million grant to help cities, companies and transportation organizations buy clean energy vehicles and install alternative fueling infrastructure. The funding is part of the DOE’s $300 million Clean Cities program, an initiative funded by the $787 billion American Recovery and Reinvestment Act. The CEC also secured another $16 million in matching funds from its partners. A nonprofit organization, CEC is dedicated to promoting clean energy technologies as a way to create healthier, energy independent communities. “The adoption of clean energy as a result of this effort will lower the long term cost and environmental impact of energy use, resulting in healthier communities that are wiser in their use of energy and more self reliant and secure in their energy supply,” says Sean Reed, CEC founder and executive director. “The grant is in line with the reach and scope of what we’re doing, but it definitely makes us a bigger player across the state.” CEC was already helping fueling station owners secure financial incentives to install ethanol pumps and compressed natural gas refueling capabilities. The federal government grant allows the organization to fund 10 new compressed natural gas stations run by DTE Energy, as well as battery-charging stations and possibly a liquefied natural gas station run by Grand Rapids-based Meijer Inc. CEC will also help its partners acquire 271 alternative fuel vehicles. CEC was formed by the stakeholders of the Ann Arbor Area Clean Cities Coalition as a new nonprofit entity to house and expand upon the work of the Ann Arbor Clean Cities program. To date, this program has successfully managed and completed over 30 state and federal grants valued at over $700,000. Among the participants in the project are the University of Michigan, the Ann Arbor Transportation Authority, and the city of Ann Arbor.
Grand Valley State University
www.gvsu.edu
During the past year, Grand Valley State University developed an action plan for its Allendale, Mich. campus to achieve climate neutrality by managing rainwater runoff, reduce consumption and recycle products. “One major initiative is the construction of large multi-cell wetlands to manage storm water,” says Norman Christopher, director of the university’s Sustainable Community Development Initiative. “Our goal is to eventually manage storm water runoff to a level similar to the conditions that existed just prior to the construction of the university.” Using rain gardens, porous pavement, buildings with green roofs, retention ponds, and underground water storage, the university will use storm water to recharge the natural groundwater reservoir and support irrigation, while creating research opportunities for students and faculty. “Our plan is being submitted in accordance with the American College and University Presidents’ Climate Commitment, which Grand Valley is a signatory,” Christopher says. “The plan encompasses all campus operations including facilities services, facilities planning, finance and administration. It will be submitted to the Association for the Advancement of Sustainability in Higher Education in January.” Grand Valley completed its first sustainability indicator report in 2005 and used it to set specific goals and target deadlines to address environmental, economic, and social concerns. “We have raised the bar and are now on a continuous improvement sustainability journey. The work never stops and it is now becoming more apparent at the citizen level, not just at the organizational level,” Christopher adds. One of the biggest challenges is reducing the consumption of resources. People on campus use products that consume large amounts of glass and plastics; both of which require energy and raw materials to make. Yet, there is not an adequate market to turn these resources into recyclable goods. In an effort to reduce bottled water consumption, the university is looking at a plan to install more water bottle filling stations on its campus, giving students and staff an opportunity to get water without purchasing another plastic bottle.
Madonna University
www.madonna.edu
Known for its academic excellence, Madonna University of Livonia, Mich. is also being a good steward of the natural world. During the fall of 2009, the university completed construction of its Franciscan Center for Science and Media, a 60,000-square-foot “green” building that it is hoping the U.S. Green Building Council will certify as meeting Leadership in Energy and Environmental Design (LEED) requirements. “We have been working diligently to complete the Kresge Foundation Challenge Grant and raise $3.25 million by Dec. 31, (2009) in order to secure a $1.5 million challenge grant for our new green Franciscan Center,” says Sister Rose Marie Kujawa, university president. “Our trustees and administrators had the vision to see that going green was the right economic and environmental decision for Madonna University today and into the future. Throughout the campus community, we look for ways to reduce our energy consumption by turning off lights as we leave the room, and encouraging staff to turn off computers when not in use. We carpool to meetings off campus, use interactive television to teach some classes in Gaylord, Orchard Lake and Southwest Detroit, distribute meeting minutes via e-mail as often as possible, print double-sided when printing is necessary, recycle paper in each office/department and use only a half sheet of paper for event or announcement postings around the University.” The green features of the Franciscan Center include: renewable and recycled materials such as glulam beams in the student gathering area, cork flooring, and paperstone counter tops. A partial green roof covered with sedum provides insulation, helps increase the roof’s lifespan, and filters pollutants and carbon dioxide out of the air. The rest of the roof is white to reflect heat and save on cooling costs. Other energy and water saving devices are: motion sensitive sinks, waterless urinals and dual flush toilets that cut water consumption by 50 percent; reverse osmosis faucets in the science labs put city water through additional softener, carbon de-ionizing, and an ultraviolet filter to neutralize 99.9 percent of bacteria; and low e-glass windows and daylight sensors for lights conserve energy. “This building not only provides a sustainable structure for our growing science and media programs, it also stands as a testament to our seriousness of purpose regarding our Franciscan value of reverence for creation,” Kujawa says. “It demonstrates our commitment to protecting the environment and being good stewards of our resources.” The building’s sustainable features and construction methods were created to limit its environmental footprint by conserving energy, water and other resources while providing a healthy learning environment and permitting safe and easy maintenance.
Society for Maintenance and Reliability Professionals Detroit / Windsor Chapter
www.smrp.org
The association created to improve to the caliber of maintenance and reliability professionals has also dedicated itself to showcasing opportunities and methodologies to reduce energy consumption and cut costs. The Society for Maintenance and Reliability Professionals (SMRP) Detroit/Windsor Chapter hosted an information-packed going green and energy cost reduction symposium in 2009 as part of its ongoing training and education activities. “We assembled a team of experts from multiple disciplines to communicate a myriad of ideas ranging from tried-and-true practices to cutting edge technologies,” notes John W. Bul, SMRP chairman of the board of directors. “The reaction to our presentations was astounding with our participants asking when additional symposiums would be scheduled.” The symposium’s topics included presentations on: global green energy savings, AmeriSource Green Initiatives, and other case studies. In addition to SMRP’s normal training seminars it is developing a “Going Green” symposium webinar series to communicate at a local, national, and international level. “We are pursuing the Going Green webinar series for three reasons including looking at asset optimization and reliability as a byproduct of sound investment and implementation of energy consumption and reduction projects,” Bul says. “It also preserves our natural resources and reduces our carbon footprint. Finally, it is the right thing to do.”
West Michigan Environmental Action Council
www.wmeac.org
![]() |
|
![]()
|
With more than 40 years of environmental education and advocacy, the West Michigan Environmental Action Council partnered with the city of Grand Rapids and other parties this past year to protect the state’s water resources. Called the Green Grand Rapids Initiative, it includes the WMEAC’s Community-Based storm water Plan to educate the public about rain gardens, low impact developments, and training individuals and groups to hold neighborhood rain barrel workshops. Through these programs, the council distributed almost 300 rain barrels in Grand Rapids. “The goal is to have the community fully and actively participate in creative solutions for storm water management and storm water policy,” says Rachel Hood, WMEAC chief executive. “The low impact development practices of rain barrels and rain gardens, developed through our water programs, managed over 6 million gallons of storm water at the end of 2009.” WMEAC developed the business-sponsored Teach for the Watershed (T4W) Program. Using hands-on science activities that meet the new Michigan Science Curriculum standards, the four-part program for teachers instructs students on the importance of protecting waterways including controlling water usage, storm water, plus information on macroinvertebrates, water quality, Adopt-A-Stream, and rain gardens. Hood explains, “Rain gardens are an easy and beautiful solution to keep storm water where it falls, instead of running off into storm drains where it carries pollutants into our rivers, lakes and streams. We helped build over 45 rain gardens in the Grand Rapids area, and have seen an increased interest among home and business owners.” The WMEAC’s Web site http://www.raingardens.org is at the top of most search engines for the keywords “rain gardens” and also provides low impact development information. The council also hosts the annual Grand River Cleanup with the cities of Grand Rapids, Wyoming, and Grandville plus community service and business partners. Volunteers beautify the river and tributaries by picking up trash along the banks. In keeping with the council’s motto, “Leading environmental protection in West Michigan by inspiring action,” its headquarters consumes less than half the energy of a comparable building due to the many green features, including a green roof and two rain gardens, making it the first zero-storm water discharge commercial site in Grand Rapids. Its operations demonstrate how money can be saved while strongly addressing environmental challenges.