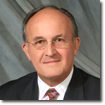
By James Partridge
Dec. 3, 2009
Employers should be concerned about indoor air quality because the productivity of their staff is directly related to their environment. The most expensive cost in the operation of a business is manpower.
What is indoor air quality? Acceptable indoor air quality (IAQ) is defined as “air in which there are no known contaminants at harmful concentrations and with which a substantial majority of the people exposed to not express dissatisfaction.” Indoor air quality issues, in all building types, can be caused by many things including, but not necessarily limited to; how the building was built, materials stored outdoors wetted prior to installation, envelope leaks, mold, inadequate outdoor air, and inadequate air filtration.
Indoor air temperature, air speed of the ventilation air, humidity, their variation, and personal parameters of metabolism and clothing insulation are primary factors that directly affect thermal comfort. However, many secondary factors may more subtly influence comfort. These include day-to- day variations, age, adaptation, gender, seasonal differences, and internal body temperature.
The built environment typically cannot be readily modified by the tenant or the building owner economically. Therefore, the more practical approach is to optimize outdoor air volumes and provide improved air particulate filtration, and ultraviolet lights for control of bacteria and viruses. The rate of outside air (OA) ventilation affects occupant health.
Available data indicates that OA supply rates are often poorly controlled. In a recent study of buildings with various rates of OA ventilation, lower ventilation rates have been associated with increased respiratory illnesses (e.g., common colds), increased sick building syndrome symptoms, and diminished satisfaction with IAQ. Also, recent data indicates that lower OA ventilation rates also are associated with small decrements in work performance. Clearly, a need exists to strike a balance between the benefits of increased OA ventilation and the beneficial energy savings from reduced OA.
An acceptable thermal environment is one in which there is a greater sense overall acceptability, basing this on 10 percent dissatisfaction criteria for general thermal comfort plus an additional 10 percent dissatisfaction that may occur on average from local thermal discomfort. A separate percentage acceptability level for the various physical variables may cause local discomfort to range from 5 percent to 20 percent.
In any built environment it is generally accepted that the occupant dissatisfaction will range between 1 percent and 10 percent; this translates into a significant amount of lost productivity as can be seen from the following example.
Assume the following; the average hourly rate per employee is $20, the overhead per employee is 2.5 times the average hourly rate, the employee works 2,080 hours per year, and there are 10 people in the office environment. The result is $1,040,000 of total payroll annually. At 1 percent dissatisfaction (that impacts productivity) this translates to $10,400 and at 10 percent dissatisfaction, the total cost becomes $104,000.
Thus, it is readily apparent that the improvement in indoor quality can have a significant impact on the success of a business by implementing low-cost modifications to the heating, ventilation and air-conditioning (HVAC) systems by incorporating improved air particulate filtration, optimizing outdoor air volumes and adding ultra-violet lights for control of bacteria and viruses.
Jim Partridge, owner of Birmingham, Mich.-based JP Consulting, has over 30 years experience as a forensics engineer and travels the country giving lectures and doing investigations.